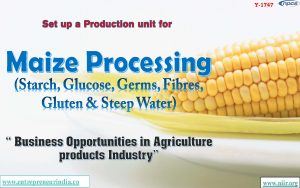
Introduction
Maize is a domesticated grass that originated in what is now Mexico around 7000 years ago. It's also known as corn, and depending on the source of data or sources consulted, both terms are used as synonyms in this study. Shortly after the European discovery of the Americas, maize spread across the globe. Corn has proved to be one of the most adaptable crops, regardless of its origin. Its evolution appears to have occurred primarily as a result of domestication, and biotypes with adaptations ranging from the tropics to the north temperate zone, from sea level to 12,000 feet altitude, and growing periods (from planting to maturity) ranging from 6 weeks to 13 months have resulted.
Related Book:- Maize (Corn) Products in India (Starch, Glucose, Dextrose, Sorbitol) Trends, Opportunities, Market Analysis and Forecasts (Upto 2017)
Between 1990 and 2011, the number of millions of hectares harvested ranged from 129.1 to 163.9 million in the United States, Brazil, Mexico, Argentina, India, France, Indonesia, South Africa, and Italy, accounting for 79 percent of global maize output. Over the same time period, maize production increased from 3.7 to 5.1 metric tonnes per hectare, and total maize production increased from 482.0 to 832.5 million metric tonnes. Domestically, 60–70 percent of maize production is used as livestock feed, while the remaining 30–40 percent is used to provide food for humans. Corn is the most widely produced cereal crop, but it ranks third in terms of staple foods after wheat and rice.
Book Link: Handbook on Maize (Corn) Processing and Manufacture of Maize Products
The reasons for this are numerous, but some are linked to cultural or social preferences, as well as the fact that corn is grown for livestock feed in some countries. More recently, the use of corn as a biofuel has sparked widespread concern about rising corn market prices, the need to expand cultivable land, as well as water quality and other environmental consequences. According to some models, large-scale corn ethanol production may result in lower food exports, higher prices, and more global deforestation.
Related Projects:- Maize, Corn and its By Products , Derivatives, Maize Processing Industry, Corn Starch, Dextrose, Liquid Glucose, Sorbitol, Oil, Gluten, Germ Oil, Wet Milling, Maize Starch Plant & related Products, High-Fructose Corn Syrup (HFCS)Projects
Maize Processing
Various maize milling machinery is used in the maize flour milling process, primarily for maize cleaning and flour milling. Automation of a scientific and fair corn flour processing process will minimise labour costs and energy consumption while still ensuring the quality of the final maize products.
Impurities Removal Process
A baffle controls the flow rate of maize kernels fed from the material inlet. When maize kernels are transported into the De-stoner by bucket elevator, they first pass through a fine sieve, where sand and other impurities smaller than maize are screened out and discharged through the taphole. Following fine sieving, maize kernels pass through a coarse filter to remove impurities larger than rice, such as corn cob flakes, which are often discharged through the taphole. It is also connected to a fan, which is located above the sieve. The aim of Fan 1 is to suck out any light impurities that may still be present in maize kernels; these impurities will be removed by centrifugal sedimentation.
Preliminary Breaking & Embryo Selection
A baffle is mounted on the storage barrel's outlet to regulate the discharge flow. When maize kernels are extracted, they are fed into a slag mill for preliminary splitting, which separates some maize skin from the embryo. The elevator then transports the damaged maize to the Embryo Selection Machine. Maize skin and embryo are split inside and expelled via various outlets. Fan 2 is attached to the top of the embryo selection machine at the same time. Some light impurities are sucked out by the fan, while the embryos discharged from the selection machine's outlet are supplied to Maize Flour Mill 1 by Suction Fan 3. The maize skins and some broken embryos that were discharged from the selection machine will be shipped to Maize Flour Mill 2.
Related Videos:- How to Manufacture Maize, Corn and its By Products
Finished Maize Flour Classification
Suction Fan 3 suctions maize flour milled by maize flour mill machine into Double Bin Sieve 1 for sieving, and Suction Fan 4 ejects the maize flour that meets requirements for weighing and packaging. While maize flour that does not meet crushing standards will be screened out of the Double Bin Sieve and delivered to Flour Mill 3 via Suction Fan 3 for further grinding. Suction Fan 3 delivers the discharged material to Double Bin Sieve 2 for sieving: Fan 4 ejects the corn flour that meets the norm, while Fan 3 delivers the substandard corn flour to Maize Flour Mill 4. Maize flour is supplied to Double Bin Sieve 2 for screening after milling.
Profile- Project Reports & Profiles
Uses
Maize is the world's most popular feed grain, particularly in developing countries. It is widely used in animal feeding and feed formulation as the primary source of calories. In comparison to other cereal grains, maize converts the driest matter to meat, milk, and eggs. Maize is a valuable feed grain because it has a high net energy content while being low in protein and fibre. It appeals to animals, who readily consume it. Maize is either fed directly or is roasted, milled, and thoroughly mixed with other ingredients. The mixture is then fed or transformed into the types that individual animals prefer. Industrial wet- and dry-milling byproducts are also used as feed.
Market Outlook
The United States, China, and Brazil are the top three producers, with the United States accounting for approximately 36% of total global production. The United States is also the leading exporter of the crop, accounting for over 36% of global exports, with Brazil, Argentina, Ukraine, and Russia following closely behind. The United States, China, the European Union, Mexico, and Brazil are all major corn-consuming countries. End-use markets such as animal feed and corn starch are supporting this rising demand in these regions. Due to the strong presence of most end-use sectors in these areas, the United States and China are among the largest consumers.
Market Research: - Market Research Report
Mexico, Japan, South Korea, the European Union, and Egypt are among the countries that depend on imports. Corn demand is increasing in the United States due to the growing feed and industrial sectors. Animal feed is the most common application in the field, followed by fuel ethanol. Corn demand is being driven by the rising corn starch processing industries in China, which is the world's leading producer of corn starch. Other application sectors where the country has a large market share include HFCS and polyols.
Capacity expansions by major key players in the industry are driving the global corn market. To increase their output, major players such as Archer Daniels Midland Co (NYSE: ADM) and Tate & Lyle Plc are expanding their production capacity and investing in mergers and acquisitions. In 2020, the global corn market will hit 1118 million metric tonnes. Between 2021 and 2026, the corn market is projected to expand at a CAGR of 5.3 percent, reaching a volume of nearly 1524 million metric tonnes.
Related projects:- Maize, Corn and its By Products , Derivatives, Maize Processing Industry
In 2020, the global corn glucose market will be worth US$ 2.1 billion. Corn glucose, also known as glucose syrup, is a food syrup made from corn starch hydrolysis. It's primarily a concentrated calorie source with no nutritional benefit. Corn glucose has become a common sugar substitute over the last few years. Corn glucose demand in the food processing industry has also increased significantly in recent years. It is primarily used as a main ingredient in commercially prepared foods to enhance flavour, improve colour, add volume, and give the food a smooth texture. Corn glucose is widely used in confectionery, preserves, tinned fruits, ice cream, sorbets, juices, dairy cakes, cookies, pastry, cereals, ketchup, sauces, vitamin tonics, and cough medicine since it prevents sugar crystallization.
In 2018, the Indian corn starch market was estimated to be worth $1.37 billion, and it is expected to expand at a CAGR of 3.9 percent from 2019 to 2024. The easy availability of corn and its wide range of applications in various industries such as food and beverage, pharmaceutical, animal feed, textile industry, paper industry, and others are driving the growth of the India Corn Starch market. The application segment of the India Corn Starch Market was dominated by the food and beverage industry. The rapid growth of India's population, as well as its rapid industrialization, has fueled the demand for corn starch.
Few Major Players:
· Aksharchem (India) Ltd.
· Amaravati Agro Ltd.
· Cargill India Pvt. Ltd.
· Devi Corn Products Ltd.
· Gayatri Bioorganics Ltd.
· Gujarat Ambuja Exports Ltd.
· Gulshan Polyols Ltd.
For More Details, Click Here: https://www.entrepreneurindia.co/project-and-profile-details/MAIZE%20PROCESSING%20UNIT
#DetailedProjectReport #businessconsultant #BusinessPlan #feasibilityReport #NPCS #industrialproject #entrepreneurindia #startupbusiness #MaizeProcessing #MaizeProduction #MaizeIndustry #MaizeBusiness #BusinessIdeas #StartupBusinessIdeas #BusinessOpportunity #CornIndustry #CornManufacturing #CornProduction