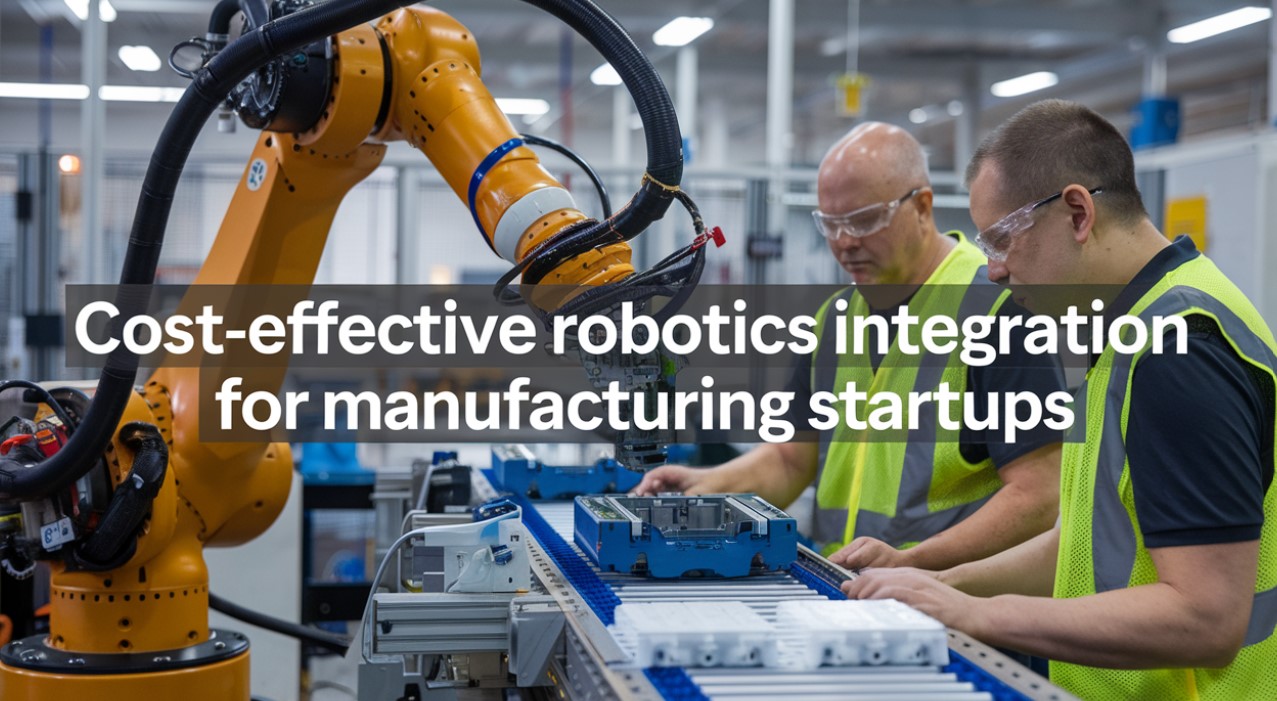
Cost-Effective Robotics Integration for Manufacturing Startups: There is competition in the manufacturing industry today; every single startup is looking for an opportunity to enhance the efficiency of their manufacturing processes, create cost reductions, and improve product quality. Robotics in manufacturing operations has become one of the most touted solutions to all these problems. However, for most small and upcoming companies, the idea of robotics in their operations might feel a little daring, given the primary costs of investment involved. The entry of robotics into the fold of a startup, if approached sagaciously, can be a paradigm shift with considerable ROI and endless future growth.
Why Robotics for Manufacturing Startups?
Robotics is no longer the privilege of big companies-it has transformed into an affordable and adaptable technology that even startups can harness. Automation can bring benefits to a manufacturing startup by
- Robots are faster and very particular in their execution of tasks relative to human workers and, hence, help to lessen manufacturing cycle time and improve throughput levels.
- Robotics can perform most tasks with a high degree of accurate results, thereby reducing defects and improving the outputs.
- Startups can automate repetitive tasks and subsequently can see reduced labor costs while improving safety and reducing human errors.
- Robotics can scale operations with business growth without high increases in labor costs or training.
Selecting the Right Model to Integrate Robotics
Once the startup has decided to integrate some form of robotics or robotics system into its manufacturing, it will move on to this next integration point: which model. Not all robots are alike, and the needs of a specific startup can differ greatly based on the manufactured product type, production scale, and budget. Here are a few common robotics models that would be more cost-effective for the start-up:
1. Cobots, or collaborative robots
These co-robots are typically affordable, secure, and simple to program. They work well for small- to medium-sized manufacturers, so bid adieu to high safety barriers and complicated programming skill requirements.
Benefits of Cobots:
- Cost-effectiveness:
- When compared to similar industrial robots, cobots typically have lower initial costs.
- Easy to reprogram for various tasks, allowing for easy production adjustment.
2. AGVs, or automated guided vehicles
These vehicles are mobile robots made to move goods and materials throughout the building. By transferring raw materials between locations along the production line or between the production line and packaging, these vehicles lessen the need for human labor in the material handling industry, improving operational efficiency and safety.
3. Robotic Process Automation (RPA) for Administrative Tasks
The RPA, especially in the case of software applications, can provide a much better substitute for automating administrative work in a manufacturing startup. Automating functions like inventory management, order processing, or payroll would free human resource applications for assignments of a more strategic nature.
Benefits of RPA:
- It costs very little to set up as compared to physical robots.
- RPA allows employees to concentrate more on value-added functions by automating repetitive tasks, further enhancing productivity.
- When the business finds more success, RPA systems can be scaled ever more easily.
RPA solutions are best suited for manufacturing startups that are looking to streamline back-office operations without investing in complex robotics systems.
Also Read: How Automation Helps Manufacturing Companies to Grow Revenue?
The cost of robotics integration
It is paramount for every startup to understand the costs associated with robotics integration. Although costs for hiring might seem outrageous, more pertinent are considerations for long-term savings and probable ROI. Here you have a list of major costs related to robotics integration:
- 1. First Cost of Purchase and Setup
Generally, robot prices differ with respective types and complexity. Such robots cost about $25,000 to $50,000, while large industrial robots cost more than $100,000. A range of $20,000 to $100,000 applies to Automated Guided Vehicles (AGV), depending on application.
- 2. Installation and Programming
Any time an overhead is incurred with a robot purchase, it has to be integrated into the ongoing production process. This may need some custom programming and setting up the required infrastructure (power supply, safety features, etc.). This may equal an added overhead of 10 to 20 percent to the total robot cost.
- 3. Maintenance and Support Costs
Regular maintenance of robots is required to keep them in good working condition. Some manufacturers offer service contracts, while maintenance itself may cost from $5,000 to $10,000, depending on the type of robot.
- 4. Training and Operational Costs
Your employees will need training to operate and maintain them, even though many robots are designed to be easy to use. This may include hiring outside trainers or having the current staff spend time learning how to use them.
Closing thoughts
By applying robotics in a manufacturing startup, one no longer sees it as wishful thinking but rather as an option within reach. The startup costs may be tremendous, but it is a wise investment considering future benefits such as increased efficiency, better quality of products, and lower operation costs. By selecting the appropriate robotics models—the cobots, AGVs, or RPA solutions that fit their operation’s careful strategies in rollout—startups can revolutionize operations all within budget. As evolving technology keeps advancing with robotics, the future of startups in manufacturing becomes cost-effective, efficient, and scalable.