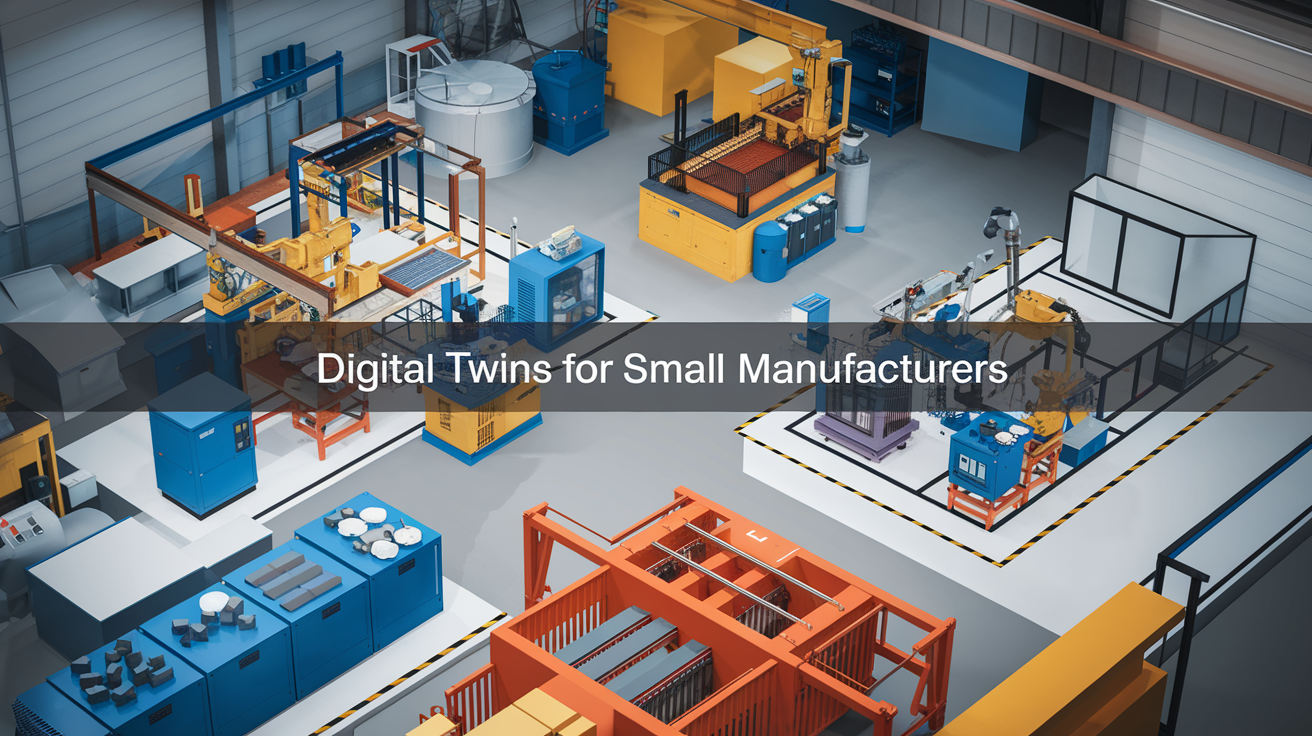
With technology transforming manufacturing, digital tools like digital twins are essential for small-scale manufacturers to stay competitive. This guide explains how to leverage digital twins effectively by highlighting their benefits in improving efficiency and decision-making. Further, it will examine the cost-benefit analysis to help businesses make smart, strategic technology investments.
Implementation Guide
Digital twins create a continuous, real-time digital copy of a physical asset or system. They capture information constantly from sensors and other sources, and in this way, manufacturing can foresee maintenance, optimize processes, and monitor performance.
1. Evaluate Business Requirements
Before embarking on digital twin technology acquisition, small manufacturers need to ascertain what they are up against and what they hope to achieve with technology.
2. Start Small with a Pilot Project
Digital twin implementations can become quite overwhelming; it is best to start with a pilot focused on one particular machine or single production process.
3. Ensure Data Integrations and Security.
Small manufacturers will be advised on the best IoT providers that consumers could work with and engage in cybersecurity measures to protect sensitive production data.
4. Train Employees and Inculcate Digital Culture.
Employee buy-in is critical for success in the application of digital twin technology. Train workers on analyzing data and handling software operations and digital workflows so they ensure that the integration is smooth, orchestrating maximum benefits.
5. Monitor Performance and Scale Gradually
Once a pilot proves successful, it will then be possible to roll out digital twin applications for the other areas of the operation. Continuous monitoring and tracking of performance will ensure successful completion in the long term.
Also Read: Solar Panel Manufacturing: Powering the Future of Clean Energy
Cost-Benefit Analysis
Cost Savings and ROI
As a result of this high initial cost, the installation of digital twins would significantly encourage savings with gains in efficiency.
Reduced Downtime
Predictive maintenance can produce a 20-30% reduction in downtimes and save thousands from idle facilities downtime.
Improved Productivity
Process optimization of 10-20% increases in efficiency levels, lowering waste and increasing outputs.
Energy Savings
The smart monitoring has saved a 5-15% energy drop in utility costs.
Lower Defect Rates
Quality monitoring reduces scrap and rework costs. It also minimizes defects brought about by real-time monitoring.
Read Our Blogs: Starting a Profitable Ceramic Tiles Business in India
Challenges and Solutions
1. High Initial Costs
Manufacturers can search for grants from government bodies or technology subsidies or lease equipment to acquire the technology without setting aside upfront money.
2. Integration into Legacy Systems
Most older manufacturing systems are not aligned with digital twin technology. Middleware solutions along with IoT gateways will help avoid corner cases for their integration.
3. Complexity of Data Management
The tremendous amount of real-time data must be saved and analyzed. The answer can be offered by cloud solutions with scalable storage systems.
4. Skill Gaps and Workforce Adaptation
Upskilling workers to new digital technologies comes as a challenge, being that it becomes slow. Training through partners and online learning platforms accelerates the readiness of the workforce.
Future Trends and Opportunities
1. AI-Powered Automation
AI will power more advanced simulations, making automated decision-making and deeper predictive insights possible for small manufacturers with their digital twins.
2. Edge Computing for Faster Processing
With edge computing, digital twins can process data as close to its source as possible, reducing latency and enabling real-time decision-making.
3. Blockchain for More Secure Operations
Blockchain can increase data security through the integration of digital twins while providing greater transparency and traceability through the supply chain.
4. Sustainability and Green Manufacturing
Digital twins will be critical enablers of achieving sustainability goals through resource optimization in manufacturing.
Closing thoughts
Digital twins are no longer the exclusive domain of large corporations. Small business ideas by manufacturers can also utilize the technology to increase efficiency, cut costs, and remain competitive. A small business should initiate digital twin implementation through a focused pilot project with the appropriate technology, keeping a close watch over costs. Investments in these technologies will pay dividends, helping manufacturers get ahead in an increasingly digital and automated future of manufacturing. With good planning and implementation, the digital twin will revolutionize smaller manufacturing enterprises into being resilient, agile, and sustainable.