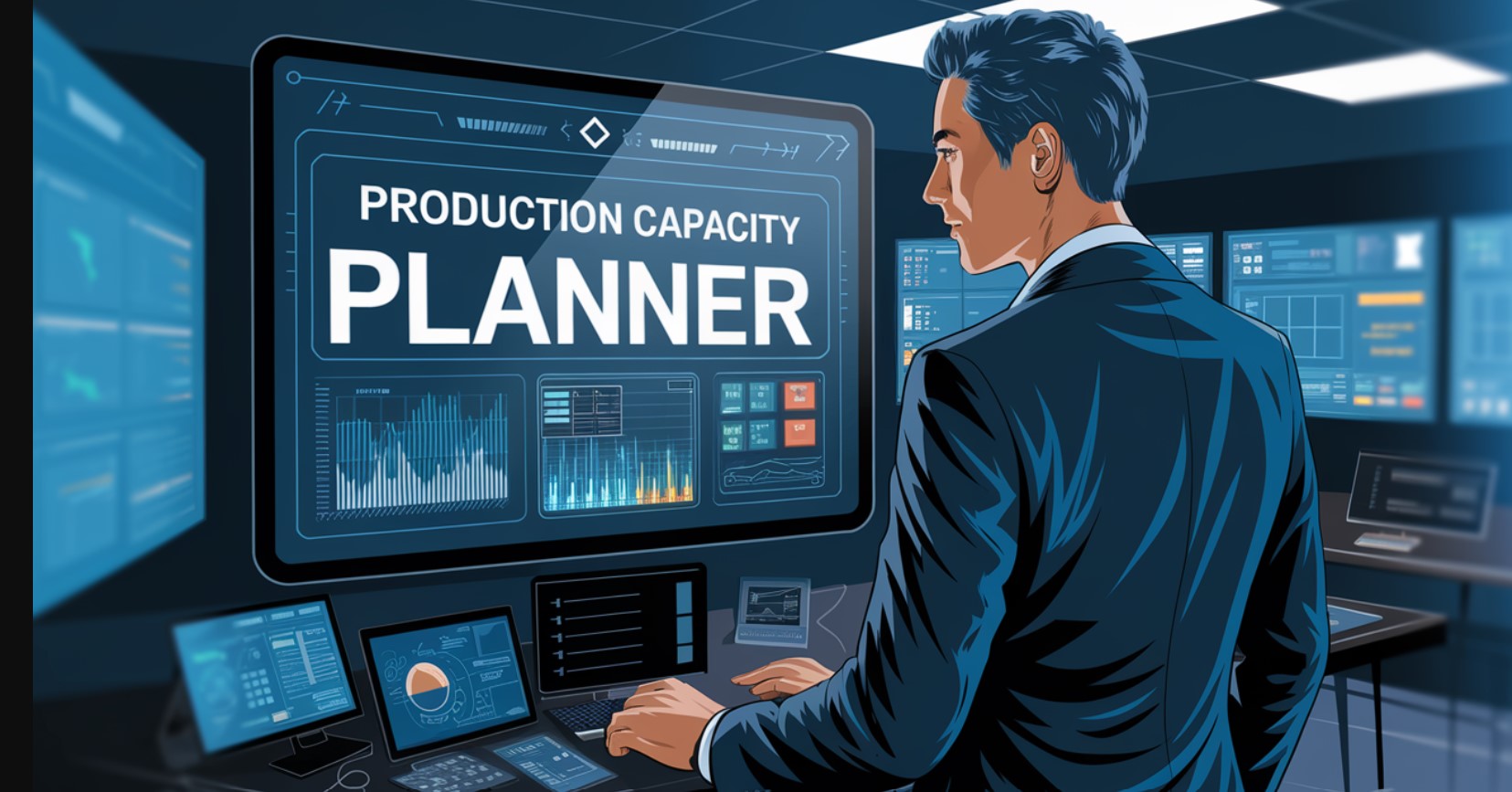
While growth signals success, it can also pose challenges for manufacturers. As demand increases, maintaining efficiency within profit margins becomes tough. Therefore, a reliable production capacity planner is essential. This guide helps you overcome growth hurdles by making data-driven decisions with ease, confidence, and long-term efficiency in mind.
Also Read: How to start a Production of Sodium Metabisulfite
Need for Capacity Planning
Many growing-stage manufacturers tend to work with low visibility of their capacity, leading to
- Missed Opportunities: Unable to fill orders for demand on account of the lack of capacity.Â
- Cost Overruns: Inefficient allocation of resources and spending on non-stated ones.Â
- Quality Issues: Producing too many products leads to a rush for some products, which results in reduced quality.Â
- Employee Burnout: Employees are pressurized and work long hours.Â
It will run your planner in a way that those things can be avoided altogether and will present in a clear, interactive way how to:
Current Capacity Evaluation: Determine accurately your present levels of production capabilities
- Forecast Demand for the Future: Prepare for possible swings in either direction.
- Optimizing Resource Allocation: Manage equipment, labor, and materials efficiently.
- Explore various growth strategies: Discuss various options to grow.
- Minimize Risks: See every possible loophole and plan for it.
Production Capacity Planner— Working
The production capacity planner works.
1. Enter your key production data:
- Product Information: Types of products and production processes under consideration.
- Equipment Inventory: Information about your machines regarding their production capacity and their utilization rates.
- Labor Resources: Information about labor with their skills and availability.
2. Analysis of Current Capacity:
- Capacity Utilization: Get a clearly defined image of your capacity utilization.
- Any barrier identification: Identify possible barriers in your operations.
- Performance metrics: Monitoring the KPIs throughout cycle time.
3. Demand Capacity Forecasting:
- Capacity Gap Analysis: Consider gaps in capacity and growth planning as well.
- Resource Forecasting: Future resource planning is about forecasting potential needs with demand forecasts.
4. Evaluate Expansion Options:
- Equipment Investment: What kind of scenario is triggered by buying new equipment?
- Increased Hiring: Evaluate the costs and benefits of hiring additional labor.
- Process Optimization: Look for areas, wherever possible, to improve processes and increase capacity.
- Outsourcing Options: Check for the possibility of outsourcing specific processes of production.
5. Optimize Resource Allocation:
- Production Scheduling: Produce and implement production schedules optimally for maximum efficiency.
- Inventory Management: Optimize inventory levels to reduce cost-outs and prevent stock-outs from occurring.
- Resource Leveling: Level out the usage of resources to prevent bottlenecks from forming.
6. Report Generation and Insight:
- Capacity Reports: It generates reports in detail on the capacity that is being utilized and measures performance.
- Cost Analysis: A study regarding the costs incurred to use varied expansion options.
- Scenario Comparisons: Compare results resulting from various scenarios, enabling informed decisions.
Read our blogs: Profitable Business Opportunity: Pectin from Apple Peels
Humanizing the Scaling Process: More Than Just Numbers
This capacity planner comes with many collaborative and communicative features, like
- Team Collaboration: Share plans and reports made with the staff.
- Task Management: Create tasks and monitor progress.
- Communication Tools: To communicate with the whole team and suppliers.
Major Scaling Challenges That Manufacturers Face:
This planner is aimed at growth-stage manufacturers and tackles the following typical challenges:
- Demand Uncertainty: Prepare for said change in demand with scenario planning.
- Resource Constraints: Resource allocation should be optimized for maximum efficiency.
- Quality Control: Provide the same quality during extremely rapid and aggressive scaling.
- Employee Training: Train employees with respect to new processes and technologies.
- Funding Constraints: Weigh the costs and benefits of alternatives for expansion strategies.
Your Growth Journey: Startup to Scale-Up
More than just a software application, the Production Capacity Planner is your partner in supporting the success of your manufacturing business, equipping you with tools and insights to make informed scaling decisions. Ways in which it helps you:
- Optimize resource allocation and minimize cost. Maximize profit.
- Enhance throughput and production processes. Enhance efficiency.
- Guarantee quality during rapid high-productivity expansion. Maintain quality through rapid expansion.
- Manage risks. Identify future bottlenecks and generate backup plans.
- Grow your competitive edge. Scale up your operations swiftly and match demand.
The Endless Growth Journey
Scaling is a process and not an event. It requires continual monitoring and evaluation. The planner allows you-
- To Monitor Performance: Monitor KPIs and highlight areas of improvement.
- To Adapt to Change: Change your plan and strategy when required.
Creating a Sustainable Future: Conscientious Development
Creating a sustainable future requires collective action, innovation, and responsible choices. By embracing conscientious development, we can ensure long-term environmental balance, economic stability, and a better world for future generations.