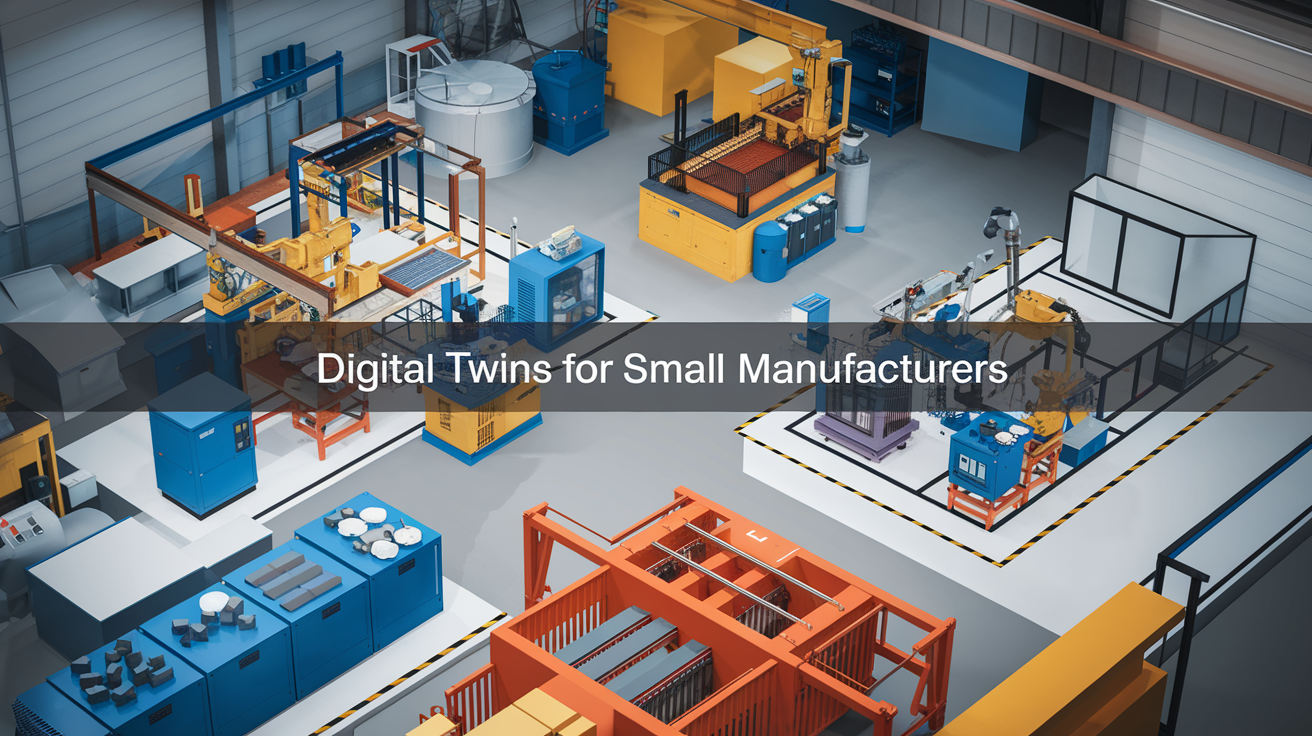
With the advancement of technologies, the way manufacturing works is changing, and it is becoming increasingly difficult to live in this present time without digital technologies, especially for keeping abreast with competitors. Another technology comprises, among others, the digital twin, with which the manufacturer can simulate, analyze, and optimize its operations in real time using virtual replicas of the physical assets, processes, or systems. While large enterprises are embracing the concept and practice of a digital twin, small manufacturers may be hesitant due to the idea of complexity and high costs involved in such processes. The fight towards adopting the technology can indeed change the game for small businesses; just because an organization might have a limitation in resource management does not imply that it should be kept out of the digital twin world. A guide on how to effectively leverage digital twins by small-scale manufacturers will be provided, along with a consideration of the equation between cost and benefits.
Understanding Digital Twins
Digital twins create a continuous, real-time digital copy of a physical asset or system. They capture information constantly from sensors and other sources, and in this way, manufacturing can foresee maintenance, optimize processes, and monitor performance.
Types of Digital TwinsÂ
Following are the types of digital twins:
- Product Digital Twins
- Process Digital Twins
- Asset Digital Twins
- System Digital Twins
Implementation Guide for Small Manufacturers
1. Evaluate Business Requirements
Before embarking on digital twin technology acquisition, small manufacturers need to ascertain what they are up against and what they hope to achieve with technology. The applications will include
- Reducing equipment downtimes by predictive maintenance.
- Improving the efficiency in production through optimized workflows.
- Enhancing product quality through real-time monitoring and automatic adjustment.Â
- Reduction of both material waste and energy usage.
2. Start Small with a Pilot Project
Digital twin implementations can become quite overwhelming; it is best to start with a pilot focused on one particular machine or single production process. This will minimize risks and yield measurable results for further scaling. Identify areas that display the most obvious lack of efficiency and where the input-output ratio of improvements is most promising.
3. Right Technology Stack for the Right Applications
For manufacturers, these include
- Sensors and IoT Devices.
- Cloud or Edge Computing.
- AI and Analytics Tools.Â
- Visualization Software.
- Connectivity Solutions.
4. Ensure Data Integrations and Security.
Small manufacturers will be advised on the best IoT providers that consumers could work with and engage in cybersecurity measures to protect sensitive production data. Encryption of data transmission, multichip authentication, and audits of systems at regular intervals would help prevent unauthorized access and the emergent cyber threats.
5. Train Employees and Inculcate Digital Culture.
Employee buy-in is critical for success in the application of digital twin technology. Train workers on analyzing data and handling software operations and digital workflows so they ensure that the integration is smooth, orchestrating maximum benefits. Cultivating an innovative, mindset-ready culture will help the teams adjust to the rapidly changing technology landscape.Â
6. Monitor Performance and Scale Gradually
Once a pilot proves successful, it will then be possible to roll out digital twin applications for the other areas of the operation. Continuous monitoring and tracking of performance will ensure successful completion in the long term. Key performance indicators like production efficiency, equipment uptime, and cost should be assessed regularly.
Also Read: Famous Entrepreneurs from West Bengal in Manufacturing
Cost-Benefit Analysis
- Investment CostÂ
The cost of digital twin implementation varies with the size and complexity of the business. It includes the following major expenses:
• Cost of IoT Sensors and Devices: $500 – $5,000 per machine.Â
• Cloud computing and storage cost: $1,000-$10,000 per year.Â
• Software and analytical tools: $2,000 – $20,000 depending on features.Â
• Training and IT Support: $1,000 – $5,000.
• Integration charges: $5,000 – $20,000 to connect old systems with digital twin platforms.
An initial total investment can range from $10,000 to $50,000 for small manufacturers, but there will be recurring spending for software licensing and maintenance, as well as cybersecurity.
Cost Savings and ROI
As a result of this high initial cost, the installation of digital twins would significantly encourage savings with gains in efficiency.
Reduced Downtime
Predictive maintenance can produce a 20-30% reduction in downtimes and save thousands from idle facilities downtime.
Improved Productivity
Process optimization of 10-20% increases in efficiency levels, lowering waste and increasing outputs.
Energy Savings
The smart monitoring has saved a 5-15% energy drop in utility costs.
Lower Defect Rates
Quality monitoring reduces scrap and rework costs. It also minimizes defects brought about by real-time monitoring.
Challenges and Solutions
1. High Initial Costs
Manufacturers can search for grants from government bodies or technology subsidies or lease equipment to acquire the technology without setting aside upfront money.
2. Integration into Legacy Systems
Most older manufacturing systems are not aligned with digital twin technology. Middleware solutions along with IoT gateways will help avoid corner cases for their integration.
3. Complexity of Data Management
The tremendous amount of real-time data must be saved and analyzed. The answer can be offered by cloud solutions with scalable storage systems.Â
4. Skill Gaps and Workforce Adaptation
Upskilling workers to new digital technologies comes as a challenge, being that it becomes slow. Training through partners and online learning platforms accelerates the readiness of the workforce.Â
Future Trends and Opportunities
1. AI-Powered Automation
AI will power more advanced simulations, making automated decision-making and deeper predictive insights possible for small manufacturers with their digital twins.
2. Edge Computing for Faster Processing
With edge computing, digital twins can process data as close to its source as possible, reducing latency and enabling real-time decision-making.Â
3. Blockchain for More Secure Operations
Blockchain can increase data security through the integration of digital twins while providing greater transparency and traceability through the supply chain.
4. Sustainability and Green Manufacturing
Digital twins will be critical enablers of achieving sustainability goals through resource optimization in manufacturing.
Closing thoughts
Digital twins are no longer the exclusive domain of large corporations; small manufacturers can also utilize the technology to increase efficiency, cut costs, and remain competitive. A small business should initiate digital twin implementation through a focused pilot project with the appropriate technology, keeping a close watch over costs. Investments in these technologies will pay dividends, helping manufacturers get ahead in an increasingly digital and automated future of manufacturing. With good planning and implementation, the digital twin will revolutionize smaller manufacturing enterprises into being resilient, agile, and sustainable.