GUAR GUM
Guar gum is found in the seeds of two annual leguminous plants (Cyamopsis tetragonalobus and psoraloides). The seeds are contained in pods 2.54 to 5.08 cm (1 to 2 in) long. In India and Pakistan, where the crop has been grown for centuries as a food for both humans and animals, hand labor is used in the harvest. In the southwestern United States, however, it has established itself with the past 30 years as a cash crop suitable for modern mechanical farm technology. The need for reliable supplies of guar gum continues to grow rapidly, and efforts are underway to establish it as a cash crop in other parts of the world.
Manufacture
The production of gaur gum in the broadest sense is a series of crushing, sifting, and grinding steps to separate the seeds from the pod and then to separate the valuable gum from the seeds. Processing techniques influence the properties and economics of guar gum ad its derivatives, and are generally held as valuable proprietary information by the various producers.
Seed Structure
The gum in contained within a portion of the seed known as the endosperm. This is the reserve food supply for the developing embryo during germination. Since the seed is dicotyledenous, two endosperm halves are obtained from each seed. These endosperm halves surround the embryo, and they are in turn surrounded by a hull, which is usually light tan in color. In some of the plant varieties, the hull is normally darker. In all varieties, there is a tendency for the hull to darken if the crop is not harvested promptly following the first frost and the next rain. In severe cases of weather damage, many of the seeds wither and turn black. The yield of gum is lowered, and the gum can be contaminated with black specks.
Guar seeds range from 0.254 to 0.635 cm (0.1 to 0.25 in) in diameter, and the endosperm is from 35 to 42% of the weight of the seed.
Purification
Endosperm is separated from the hull and embryo by taking advantage of the difference in hardness of the various seed components. Multistage grinding and sifting operations are combined with other physical treatments to crack the seeds and separate the parts. There are many types of grinders, such as attrition mills and special types of hammer and roller mills, that can be employed in combination with water or acid soaks and embrittling heat treatments.
Grades
The endosperm is ground, to powder form and marketed as guar gum.
Food-grade. Substantially but not completely pure endosperm is obtained by the usual commercial purification techniques. There may be a small amount of hull and germ present, owing to imperfect purification. Since the entire seed is edible, this contamination dilutes slightly the amount of available gum, but does not harm its suitability as a food additive. See Tables 1 and 2 for Food Chemicals Codex specifications any typical analysis.
Determination of moisture, protein, and acid-insoluble residue content is generally considered to be the minimum analysis needed to monitor the efficiency of the purification process. The presence of the germ is reflected in high protein content. Hull fragments show up as a high acid-insoluble residue. Moisture contents above 15% or below 8%.
TABLE - 1
Food Chemicals Codex Specifications for Guar Gum
Galactomannans: Not less than 66.0%
Limits of impurities:
Acid-insoluble matter: Not more than 7%
Arsenic (as is): Not more than 3 ppm (0.0003%)
Ash (total): Not more than 1.5%
Heavy metals (as Pb): Not more than 20 ppm (0.0002%)
Lead: Not more than 10 ppm (0.001%)
Loss on drying: Not more than 15%
Protein: Not more than 10%
Starch: Passes test (negative)
TABLE - 2
Typical Analyses of Guar Powder
| Food-grade fine mesh | Food-grade Intermediate mesh | Food-grade coarse mesh | Industrial-grade fine mesh |
Percent moisture |
10-12 |
10-12 |
10-12 |
10-12 |
Percent protein |
4-6 |
4-6 |
4-6 |
4-6 |
Percent acid insoluble residue |
2.5-5.5 |
2.5-5.5 |
2.5-5.5 |
2.5-5.5 |
Viscosity :* Pa's |
3-5 |
2.5-4.5 |
2-3.5 |
3-5 |
cP |
3000-5000 |
2500-4500 |
2000-3500 |
3000-5000 |
*At 25oC as measured on a Brookfield Synchro-Lectric viscometer at 20 rpm.
exceed normal equilibrium moisture and indicate abnormal treatment of the seed or powder.
A crude fiber determination is sometimes used in place of the acid-insoluble residue. Crude fiber is the acid and alkali-insoluble residue and typically amounts to about half of the acid-insoluble residue. It is recognized that other natural impurities are present in food-grade guar gum. The natural mineral content of the seeds gives rise to an ash content. Low molecular-weight soluble sugars are present but not usually assayed, and a small ether extractable fraction reflects the natural presence of fats and oils.
Industrial-grade. Historically, most of the guar gum sold for industrial applications has been made from endosperm as pure as that used for food-grade products. Industrial grades however, make extensive use of chemical additives to modify and control such properties as rate of swell, viscosity, and solution stability for specific end uses. These additives can lead to controlled gelation and controlled viscosity decrease.
Processing techniques can also control dispersion, rate of hydration, and viscosity. When these techniques are combined with the use of chemical additives, they lead to the historic pattern of tailor-made products which has dominated the growth of guar consumption.
Derivatives. In recent years, anionic (carboxymethyl), non-ionic (hydroxyalkyl), and cationic (quaternary amine) derivatives have become important factors in total guar consumption. These derivatives are not presently approved for food use, although some may be in the future. The development of the derivatives has followed the pattern previously noted for industrial-grade products. That is, they make full use of chemical additives and processing techniques and are designed to satisfy specific customer enduse requirements. Many produts are currently available, and their number and importance are growing rapidly.
Chemical and Physical Properties
Guar gum is a carbohydrate polymer containing galactose and mannose as the structural building blocks. The ratio of the two components may vary slightly, depending on the origin of the seed, but the gum is generally considered to contain one galactose unit for every two mannose units.
Structure
It has long been accepted that the structure of guar gum is a linear chain of b-D-mannopyranosyl units linked (1Ã 4) with single-membered a-D-galactopyranosyl units occurring as side branches. The a-D-galactopyranosyl units are linked (1 Ã 6) with the main chain. Recent work has confirmed the long-held belief that the side branches are spaced uniformly. Guar gum is a natural alternating copolymer, as shown in Fig. 1.
All of the commercially important derivatives of guar are formed by etherification. The primary C6 hydroxyl position is the most highly reactive, but the secondary hydroxyls are also sites or substitution.
Solubility in Water
Guar gum is a cold water-swelling polymer. In its powdered commercial form the rate of thickening and the final-viscosity reflect the process history of the product, including the particle size of the powder. See Fig. 2 for typical swell curves of a range of available products.
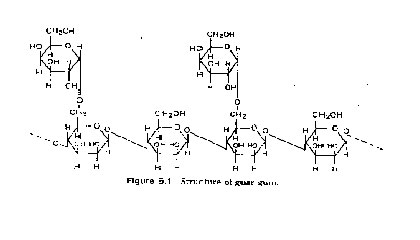
Heating a guar gum solution reduces the time needed to reach its full viscosity potential.
Water is the only common solvent for guar gum, although it will tolerate limited concentrations of water-miscible solvents, such as alcohols. Dimethylformamide and dimethylsulfoxide are solvents as they are for most other polymers.
Commercial guar gum solutions are typically turbid. The turbidity is largely caused by the presence of insoluble portions of the endosperm. Polymer solutions, intensively purified in the laboratory by noncommercial methods, approach water clarity.
Derivatives of guar gum can show dramatically different solubilities and clarities in solution. There are hydroxyalkyl derivatives available, much clearer than guar gum, capable of tolerating major proportions of water-miscible solvents. Carboxymethyl derivatives in general are much clearer than guar gum. Improved clarity results from derivatization and solubilization of insoluble seed impurities. Changes in solubility occur when sufficient hydroxyl groups of the galactomannan are substituted and the new polymer takes on some of the characteristics of the derivatizing reagent.
Rheology
Guar gum is one of the most highly efficient water-thickening agents known. Solutions of guar gum and its derivatives are non-Newtonian, classed as pseudoplastic. They thin reversibly when heat is applied and degrade irreversibly with time when an elevated temperature is maintained. Some of the recently developed hydroxy-alkyl derivatives resist such degradation to a much greater degree. Solutions resist shear degradation well compared to other water-soluble polymers, but they will degrade with time under high shear. Figures 1.2 show viscosity and shear properties of guar gum.

Fig. 2: Viscosity development as a function of time for typical guar products. Solution concentration is 1% in water (Measured on Brookfield Synchro-Lectric viscometer at 20 rpm, 25oC)
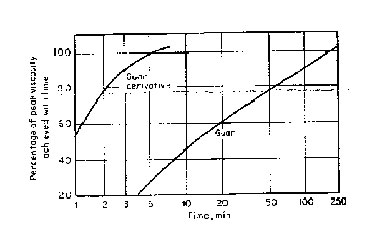
Fig. 3: Percent viscosity developed as a function of time for typical fast hydrating guar and guar derivative types. Solution concentration is 1% in water. (Measured on a Brookfield Synchro-Lectric viscometer at 20 rpm, 250C.)
Viscosity. Guar gum and its derivatives are most commonly used at concentrations below 1%. High-viscosity products are thick solutions at this concentration and look more like gels at 3%. Guar and guar derivatives are available in lower-viscosity form for special applications, for example, where high gum solids are favored, where it is desirable to have charged molecules with controlled thickening power, or where less pseudoplastic, more Newtonian solutions are appropriate. The wide range of viscosities commercially available is consistent with the historic approach of designing guar products to meet the needs of an industry. See Table-2 for the range of typical products.
Shear Response. Solutions of guar gum have zero yield value at the most commonly used concentrations. That is, they begin to flow as soon as the slightest shear is applied.
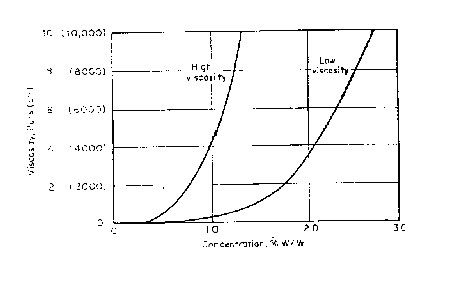
Fig. 4 : Effect of concentration on the viscosity of typical high-and low-viscosity guar products.(Measured on a Brookfield Synchro-Lectric viscometer at 20 rpm after 24 h hydration at 250C.)
Reactivity
The cyclic neutral sugar structures which make up the polymer contain numerous hydroxyl groups (an average of three per sugar unit). The various reactions of guar gum with other substances are explained by the number and position of these hydroxyl groups.
Derivatives. Etherification and esterification reactions are readily carried out through the hydroxyl functionalities. The commercially important derivatives to date have been confined, however, to the etherification reactions: carboxymethylation with monochloroacetic acid, hydroxyethylation with ethylene oxide, hydroxypropylation with propylene oxide, and quaternization with various quaternary amine compounds containing reactive chloride or epoxide sites.
Significant changes in properties occur when the guar molecule is substituted with these reagents. The degree of change is a function of the type of reagent, the amount of reagent, and the conditions of reaction.
Inclusion of charged sites into the guar molecule is a most obvious source of change. Anionic sites (carboxymethylation) and cationic sites (quaternization) modify the way in which the guar molecule reacts with inorganic salts, hydrated mineral and cellulosic surfaces, and organic dyes. Many products have been designed to take advantage of these changes for specific applications. Depending on the need, the rate and degree of adsorption can be strengthened or lessened, flocculation increased or decreased, gelation made easier, and compatibility improved. Carboxymethylation has the added effect of improving the clarity of guar solutions by solubilizing some of the non-guar seed impurities that result from commercial processing.
Changes in solubility in and compatibility with water-miscible solvents are particularly promoted by hydroxyalkylation. For example, dramatic increases in alcohol tolerance are seen with increasing derivatization.
Hydroxyalkylation is a very useful tool for changing the way in which guar reacts with hydrated mineral and cellulosic surfaces. Increasing degrees of derivatization have the effect of lessening the affinity for such surfaces. This leads to compatibility with high-solids mineral dispersions, modified flocculation rates in complex ore dispersions, and easier removal of gum from dyed fabric by way of illustration.
Electrolyte compatibility is extended by hydroxyalkylation (see Table 6.3), Derivatives have been designed to thicken di- and trivalent salt solutions in which guar will fail to hydrate.
TABLE - 3
Electrolyte compatibility of Guar vs. Hydroxypropyl Guar
Viscosity measured on a Brookfield synchro-Lectric viscometer at 20 rpm. Solutions at 1% concentration based on weight of salt solution, 25OC
<th colspan='2' align='center'>Viscosity, Pa's (cP)<td colspan='2'>Guar<td colspan='2'>Hydroxypropyl guar
|
|
26% NaCl |
9.1 |
(9.100) |
9.45 |
(9,450) |
38%CaCl2 |
0.02 |
(20) |
7.7 |
(7,700) |
56% Ca (NO3)2 |
0.035 |
(35) |
22.55 |
(22.500) |
Biodegradability is progressively changed with increasing hydroxyalkylation. Guar which is easily degraded can be made highly resistant and stable in viscosity with suitable substitution.
The solubility and clarity of guar solutions are markedly improved by hydroxyalkylation. As with carboxymethylation, it is believed that this is a result of derivatizing and solubilizing seed impurities, particularly the cellular components of the endosperm.
Mixed ethers of the various reagents are used to combine the benefits of charged and uncharged substitution for specific applications.
The central conclusion to be drawn from the preceding discussion is that guar gum has proved to be an excellent polymeric raw material for the creation of new and important water-soluble gums. In the process, the range of problems that can be solved has been greatly expanded. The outlook is for a continuing flow of new products in the years ahead. These products will provide increasingly more sophisticated answers to major industrial needs.
Borax Reaction. Each of the sugar residues in the polymer has two hydroxyl groups positioned in the cis- form. This leads to an interesting and valuable reaction with dissociated borate ions that is characteristic of such polymers. The reaction is fully reversible with changes in pH. An aqueous solution of the gum will gel in the presence of borate when the solution is made alkaline, and will liquify again when the pH is dropped below 7. If the dry powdered gum is added to alkaline borate solution, it will not hydrate and thicken until the pH is dropped below 7. The critical pH at which gelation occurs is modified by the concentration of dissolved salts. The effect of dissolved salts is to change the pH at which a sufficient quantity of dissociated borate ions exists in solution to cause gelation.
Derivatives of guar gum tend to react less and less with borate ions as the amount of substituting groups increases in the molecule. This results because the shear bulk of substituting groups changes the regular, alternating, and single-member branched, linear configuration of the molecule and prevents adjacent chains from approaching as closely as before and the substitution of secondary cis-hydroxyl positions decreases the number of such unsubstituted positions available for reaction.
Gels. A considerable number of reactions other than the borax reactions are routinely used to convert guar and guar derivative solutions to gels. These gels may range from pumpable high-viscosity compositions to solid, rubbery products. The common factor is that they are formed by transition metal complexes through the cis-hydroxyl positions. Derivatization alters the strength of the gels in the same way that it affects the borax reaction.
In the special case where a relatively minor amount of charged substituent (e.g., carboxymethyl) has been introduced into the molecule, this can serve as a useful site for ionic crosslinking of adjacent chains.
Salt Reactions. Strong reactions are also obtained with solutions of certain inorganic cations. The addition of a high concentration of calcium salt, for example, will cause a gel to form under alkaline conditions. If dry powder is added to the salt solution, the gum will not hydrate and thicken. In general, the gum will react with polyvalent cations much as it does with borate anion. Significant differences, however, are that many of the reactions lead to insolubilization, precipitation, or unstable, non-useful gels.
Derivatization with non-ionic hydroxyalkyl groups greatly improves the compatibility of guar with most salts.
Biological Properties
Guar gum has the status of a direct food additive. Solutions of guar gum serve as a food source for the growth of common microorganisms. Where it is necessary to hold solutions for a length of time, common food preservatives, such as benzoic or sorbic acid, may be added to inhibit bacterial growth. In non-food applications, quaternary ammonium preservatives, chlorinated phenolics, or formaldehyde are effective bacterial inhibitors.
The advent of guar derivatives as important commercial products has brought another technique for the preparation of stable solutions. Substitution of the hydroxyl groups alters the structure of the molecule and makes it less suitable as a food for common microorganisms. The more the molecule is altered, the more resistant it becomes to biological attack. The derivatives in wide use today are more resistant than guar to a significant degree. The outlook is for the introduction of derivatives that are stable in solution for long periods of time. They will even resist inoculation with potent cultures that would destroy a guar solution within an hour.
Pending the introduction of completely stable derivatives, in those cases where the bacterial contamination has been allowed to get out of hand and manufacturing equipment contains the residue of preceding batches, it is much easier to thoroughly clean the equipment and start again than to try to control fermentation with preservatives.
Handling
Consideration of the storage of the powdered product and preparation of guar solutions follows:
Dry Storage
The powdered commercial grades of guar gum and its derivatives are all stable in the dry form. In common with other water-soluble polymers, the one condition that adversely affects the gum is allowing it to get wet. As long as it is stored in a dry place, there should be no problem from fermentation or lumping of the powder.
Solution Preparation
Many techniques are available to form smooth, uniform solutions from these cold-water-swelling powders. The principal need is to uniformly disperse and wet each particle. Particles that are not properly separated will stick together as they begin to swell, leading to lumpy, nonhomogeneous solutions requiring abnormally vigorous agitation and time to come to a uniform, fully hydrated state.
Vigorous agitation is the most common means of dispersing rapidly swelling powder. Additional flexibility can be had by selecting coarser-mesh products that swell less rapidly. If other powders are to be added to a solution, the gum may be preblended with these powders, which will assist in ease of dispersion. Similarly, liquids that must be added to a formulation can serve as a carrier for the gum, providing the gum does not swell in the liquid.
For the really difficult cases where agitation is poor and the gum must be added directly to water, there are chemical means to briefly retard the hydration of even the finest-mesh, fastest-swelling gum. These techniques are suitable only for industrial products. Such products are routinely supplied by the manufacturers to meet the specific needs of a customer.
Applications
Guar gum and its derivatives are among the most important water-soluble polymers. Major uses are in the oil and gas, textile, paper, food, explosives, and mining industries.
Oil and Gas
It is common industry practice to increase the productivity of oil and gas wells by cracking open the hydrocarbon-bearing zones with hydraulic pressure. Guar and its derivatives are used in this process, which is known as hydraulic fracturing. High viscosity, at reasonable cost, is required to carry the graded sand which is pumped into the fractured rock. The sand props open the fracture when the hydraulic pressure is released. Oil and/or gas is then recovered at an increased rate because the porous rock containing the hydrocarbon has much more surface area exposed and connected to the well bore through the fracture channels just formed.
Guar products provide the viscosity needed for this operation. They are also compatible with a wide range of field waters and can be formulated to lose viscosity at a controlled rate. This facilitates removal from the well bore when flow is reversed upon completion of the job. Guar products are also useful in controlling fluid lost to the porous formations being fractured and in reducing frictional pressure losses while fluid is being pumped.
Explosives
The last 20 years have seen the growth of a sophisticated technology which uses nitrate salts, various organic and inorganic sensitizing ingredients, water, and a water-soluble crosslinkable thickener as a means of making what are called either slurry explosives or water gel. These compositions are safer to use than previous explosives and have been formulated to meet such a variety of application needs that they are often the most economical way of formulating an appropriate explosive.
Guar gum and its derivatives are used in the formulation of such products. It is the ability of guar products to thicken efficiently under a variety of difficult conditions and to be readily crosslinked or gelled that makes them useful. A properly formulated slurry explosive gel may be anything from a rather loose, cohesive, and pourable gel to a rubbery, almost rigid solid.
Textile
Guar and its derivatives are used as dye solution thickeners in textile printing applications. The derivatives are primarily carboxymethyl and hydroxylalkyl ethers of guar. They are often oxidized under controlled conditions so that the thickening power of the product vs. concentration is brought to a predetermined level. Derivatization promotes solubility. This is useful in preventing the buildup of guar and its derivatives on printing screens and aids in their removal by washing after printing.
Food
This industry has made wide use of guar gum's ability to bind large amounts of water.
Ice Cream. Small amounts of guar gum do not greatly affect the viscosity of the mix during manufacture, but impart a smooth, chewy texture to the finished product. A show meltdown of the product and increased heat shock resistance are other benefits. Ice cream stabilized with guar gum is notably free of the graininess caused by ice crystal formation.
Canned Pet Food. High free-water content is characteristic of this type of product. Guar gum is used to thicken the free water in the product, and the meat and vegetable solids are coated with a thick gravy. Special, slow-swelling grades of guar gum are sometimes used to limit viscosity during the can-filling operation.
Cheese. In soft cheese processing, guar gum controls the consistency and spreading properties of the product. Smoother, more homogeneous cheese spreads with high water content are possible because of the gum's water-binding properties.
Sauces and Salad Dressings. These products make use of the high viscosity at low concentration that is a basic property of guar gum.
Paper
The major use of guar gum is as a wet-end additive. This means that the gum is added to the pulp suspension just before the sheet is formed on either a Fourdrinier machine or a cylinder machine. The pulping process, which is designed to remove lignin and thereby produce a fibrous cellulosic pulp, also removes a large part of the hemicelluloses normally present in the wood. These hemicelluloses, which are mostly mannans and xylans, could contribute greatly to the hydration properties of the pulp and the strength of the paper formed from the pulp. Galactomannans replace or supplement the natural hemicelluloses in paper bonding.
It is generally agreed that the hydrogen-bonding effect is one of the major factors affecting fiber-fiber bonding. An examination of the molecular structure of galactomannans reveals a rigid long-chain polymer molecule with primary and secondary hydroxyl groups. Such molecules are capable of bridging across and bonding to adjacent fibers.
It is difficult to compare the efficiency of locust bean gum and guar gum in paper products because too many variables exist, such as type of gum formulation, pulp type, beating time, and machine conditions. However, many persons in the paper industry believe that guar gum is the more efficient additive.
Commercial locust bean gum and guar gum contain small amounts of hull as contaminants. Locust bean hulls are red-brown and in white sheets, and appear as small but visible specks. However, guar hull is almost white. When present in the paper sheet, it is indistinguishable from the bleached pulp.
Advantages gained by the addition of galactomannans to pulp are:
- Sheet formation: A more regular distribution of pulp fibers (less fiber bundles) improves sheet formation.
- Mullen: Mullen bursting strength is increased.
- Fold strength: Fold strength is increased.
- Pick: Pick is a measure of the force required to pull a fiber from the surface of a sheet. It applies to printing grades of paper. Pick is increased.
- Pulp hydration: Pulp is normally passed through jordans or wet mills which increase the surface of the fiber, thereby allowing it to bind more water. Galactomannans added to a pulp aid in the binding of water and decrease the amount of refining necessary, thereby lowering power consumption.
- Finish : Finish is improved, as measured by the smoothness and amount of protruding fibers.
- Porosity: Porosity is decreased.
- Flat crush: The pressure required to crush a corrugated flute is increased.
- Machine speed : Machine speed is increased without losing desirable tested properties.
- Retention of fines : Retention of fines is increased. Recently, cationic derivatives of guar have been developed with outstanding ability to increase drainage and fines retention.
Mining
In this industry, guar gum and its derivatives are widely used as flocculants to produce liquid-solids separations. These may be broadly classified as filtration, settling, or clarification of mineral slurries. The property used is the ability of the gums to adsorb on the hydrated mineral particles by hydrogen bonding, followed by agglomeration as a result of bridging. Guar gum is also used in flotation to recover base metals. Guar gum acts as a depressant for talc or insoluble gangue mined along with the valuable minerals.
As an illustration of the use of guar products as flocculants, consider the case of an ore ground to a desirable particle size, leached to solubilize a valuable mineral, and then fed to a series of thickeners to separate the pregnant solution from fine solid waste. When dilute guar solutions are added to the leached ore, settling takes place within the thickeners. The rate at which this process takes place is governed by the slowest settling velocity in the thickeners. In turn, this depends on particle size, which is governed by the ability of guar molecules to form large flocs by first adsorbing on the hydrated solids and then causing them to agglomerate by bridging.
Settled solids flowing from the thickeners may be further dewatered by filtration. Guar products increase the permeability of the filter cake, resulting in an increased filtration rate. The floc formed is also incompressible and is readily penetrated by wash water. The cake is readily handled and transported by conveyor belts without decrepitation or dusting. The pregnant solution of this illustration may be further clarified before passing to metal recovery by treating it with dilute guar solution and allowing flocculated solids to settle, leaving behind clarified supernatant.
The terms settling, filtration, and clarification, then, usually relate to the individual steps of an overall mining recovery or wastewater treatment operation, and the terminology is governed by the intent of the particular step in that operation. Improvement of the operation by flocculation of solids is the common denominator.
In flotation operations the ore is ground to a desirable particle size and slurried in water prior to treatment. When guar or guar derivative is added as a dilute solution to the slurry, the gum adsorbs on the hydrated surfaces of the unwanted talc or gangue. Reactive chemicals called collectors are then added to the slurry and they react with the desirable minerals rather than the talc or gangue. The collectors condition the mineral surfaces so that the minerals will rise to the surface when a frother is added and air is bubbled through the slurry. Froth is skimmed off, separating the values from the talc or gangue that has been depressed by the guar product.
COMMERCIAL APPLICATIONS: Compounding and Formulating
The use of guar gum products is primarily in food or explosive applications.
TABLE - 4
Maximum Usage Levels Permitted
Food (as served) | Percent |
Baked goods and baking mixes |
0.35 |
Breakfast cereals |
1.2 |
Cheese |
0.8 |
Dairy products analogs |
1.0 |
Fats and oils |
2.0 |
Gravies and sauces |
1.2 |
Jams and jellies |
1.0 |
Milk products |
0.6 |
Processed vegetables and vegetable juices |
2.0 |
Soups and soup mixes |
0.8 |
Sweet sauces, toppings, and syrups |
1.0 |
All other food categories |
0.5 |
Food
Table-4 lists permissible use levels under FDA regulation 184.1339.
No stabilizer is composed entirely of guar gum. Guar derivatives are not presently permitted in food products. Use of the gum is further regulated under Section 170.3 of the Food and Drug Administration as to its function in specific food products.
Explosives
Slurry explosive formulations are best left to those skilled in the art, working under properly controlled conditions.
COMMERCIAL USES: Processing Aids
Oil and Gas
An oil or gas well can be fractured with a solution containing up to about 1% (by weight) of a guar product by supplying sufficient hydraulic horsepower to overcome the overburden pressure and crack the rock. The fracture thus formed is extended outward as far as possible by maintaining pressure and pumping the fluid, which contains graded sand, into the fracture. The sand props open the fracture when the operation is complete.
Textile
As discussed earlier, guar and guar derivatives are widely used in printing and dyeing applications as thickeners to control the mobility of dyestuffs. In some cases the viscosity they develop controls the volume of dye feed. The derivatives are largely hydroxyalkyl and carboxymethyl products, sometimes oxidized to varying degrees to control their thickening power. Locust bean gum products compete directly with guar gum products in this area, and the choice is usually governed by economics since such things as flow, viscosity, and solubility can be altered at will.
The following discussion of applications in the carpet industry illustrates the wide range of techniques in current practice. Similar techniques would apply to flat goods after taking into account the differences in construction of flat goods vs carpets.
Carpets
There are two use areas for gums in the carpet industry; one is dyeing and the other is printing. Some carpet yarns (primarily the spun yarns) are stock-dyed or package-dyed. In package-dyeing, gums are used at very low concentrations (0.1 to 0.2%) as migration control agents to produce a more even distribution of dye in the package.
Most of the carpet yarns are dyed after the carpet is formed, either by the beck method, or where long runs of the same shade are involved, by the newer continuous-dyeing machines. Beck dyeing is done by the exhaustion of dyes onto the fiber and requires no gum, but with one exception all of the newer continuous-dyeing machines use gum as the viscosity control to regulate the pickup of dye on a polished stainless steel roller immersed wire dye peed pan. This film of dye is continuously knifed off and cascaded in a sheet across the width of the carpet just prior to the fixation process, which takes place in a steaming chamber. During the steaming operation, the gum content of the dye solution serves to control the migration of the dye molecules so that a level shade is obtained from side to side of the carpet and also from the surface to the backing of the carpet.
Very-high-viscosity gums are used in this application so that an extremely low percentage of gum can be employed to maintain the critical viscosity level. The actual viscosity of the dye solution is low, in the range of 0.02 to 0.03 Pa.s (20 to 30 cP), and the concentration of gum used is in the area of 0.20 to 0.25%. This low level of gum is an advantage since there is less gum to wash off after the dyeing operation.
Carpet printing is done by various methods and the gum requirements vary with the method. Space printing is a technique originated some years ago. Essentially space printing is the production of a completely random distribution of a number of colors to produce a "pepper and salt" type pattern. The original patented process consisted of printing a geometrical distribution pattern on either flat or tubular knotted fabric and, after fixation of the color, deknitting and winding on cones. This printed yarn was then supplied to tufters to produce the patterned carpet. Other methods have been developed to produce similar effects by warp sheet printing, splatter printing of droplets of color, and computer-programmed distribution of color through nozzles or by pressure bars.
All of these methods require a gum thickener, and the thickener must have very special characteristics for optimum performance. The thickener should be low in insolubles content, high in viscosity, easily dispersible to a lump-free paste, extremely soluble for easy washout, produce good apparent color value, and be compatible with auxiliary chemicals and dyes being used.
Gums for space printing are generally used at 0.35 to 0.5%, and the viscosity will be 0.25 to 0.5 Pa.s (250 to 500 cP), depending on the method, fiber, and pattern.
Pattern designs on carpet are produced by two different screen printing techniques; the first and oldest method is by use of flat screen stencils, and the second is by means of rotary screen stencils which are tubular in shape and made of metal, such as nickel or stainless steel.
The flat screen method is somewhat slower than rotary printing but has a wider range of pattern choices. It also takes up more floor space. But if screen damage or blockage should occur, it is easier and quicker to rectify, and so produces less damaged carpet. Flat-bed machines run at speeds in the range of 4.6 to 6.1 linear meters (15 to 20 feet) per minute for most patterns and types of carpet, while rotary machines are capable of speeds of 18 linear meters (60 feet) per minute, or more. Flat-bed machines use medium-viscosity gums for most patterns and may use high-viscosity gums at lower solids under certain special conditions or on certain pattern or carpet types. Rotary machines can run most patterns on the more economical high-viscosity gums, but do require medium-viscosity gums for finer line patterns.
Flat-bed machines generally operate with dye pastes in the range of 0.8 to 7.5 Pa.s (800 to 7500 cP) viscosity depending on the pile type and pattern. The gum percentages may be anywhere between 0.75 and 3%, depending on the type gum and viscosity requirements.
Rotary machines operate in a narrower range of viscosities, 6.5 to 10 Pa.s (6500 to 10,000 cP) using gum concentrations of from 1.25 to 2.5%, depending on the gum type and viscosity requirement.
There are several printing machine types which do not fit the description of either the flat-bed or rotary which are also capable of producing pattern effects. These are : (1) the modified roller type which uses raised patterns on a series of rolls arranged radially around a central cylinder, (2) the jet nozzle type which feeds color through jet tubes programmed to produce the pattern required, (3) the reverse dip method machine which feeds carpet with the pile face down and applies color by compartmented reservoirs which rise and fall as the carpet traverses, and (4) the pressure bar segmented rollers machine which prints a warp sheet of yarn run between a number of pairs of such rolls using one pair of rolls for each color. These machines all use relatively low-viscosity dye pastes made up with high-viscosity gum at low solids. The gum viscosities will vary from 0.05 to 0.3 Pa.s (50 to 300 cP), and the gum concentration will be in the range of 0.3 to 0.5%.
This area of carpet processing is growing rapidly and innovations are the rule rather than the exception in this particular segment of dye application.
The viscosities mentioned are all by Brookfield RVF Model using the appropriate spindle at 250 C and 20 rpm. Viscosities measured by other means will be considerably different.
Paper
Naturally occurring hemicellulosics, which promote hydration and play an important role in interfiber bonding, are removed during the pulping process. To supplement and replace hemicellulose, the most suitable polysaccharides have proven to be the galactomannan gums, guar and locust bean.
In general, there are two ways to prepare guar or locust bean gum for use; either by cooking or by dry addition.
For mills that do not have and do not wish to install cooking equipment, specially processed products which can be added dry to the beaters or pulpers are available. These products are formulated for ease of dispersibility in the stock, and designed to suit the specific conditions of stock preparation, i.e., temperature, pH, and retention time. They develop full hydration while in the stock at specific rates determined by individual product design.
However, most mills find it easier and more practical to prepare solutions of guar or locust bean gum before addition to the pulp slurry. This enables them to maintain a finer control on the amount of gum being added to their pulp system and also allows them to quickly increase or decrease the amount of additive as needed.
Guar or locust bean gum solutions are prepared by one of two methods: the batch system or a continuous cooking system. Solutions can be prepared in the batch system by dispersing 0.5 to 1.0% of the dry powder in cold water under mechanical agitation, and then heating the dispersion to 900 C to 96°C (195 to 205o F), holding the solution at that temperature for 10 to 20 min. the benefit of a continuous cooker is the preparation of a gum solution on an automatic, continuous basis with lower manpower requirements.
After preparation of guar or locust bean gum solution, it can be added at any convenient point in the stock system that lies after the point of refining and provides good distribution. Since these materials have such a high affinity for adsorption on cellulose, it is recommended that the solution be diluted as much as possible before addition so that a more uniform distribution rate of gum to cellulose can be accomplished.
In most mills, addition in the vicinity of the fan pump offers the best control of the additive process. The rate of delivery of the prepared guar or locust bean gum to the paper machine can best be regulated by use of a rotameter. The normal requirement for attaining measurable improvements is in the range of 1 to 6 kg/metric ton (2 to 12 lb/ton) dry basis, but conditions of the pulp furnish, basis weight, machine speed, stock freeness, etc., will ultimately govern the proper level of addition.
The general benefits gained through the use of guar or locust bean gum vary with the particular paper product being manufactured.
Kraft Papers
A growing use of gums by makers of multiwall bag and gumming grades of kraft paper has shown specific improvements. The rate of addition varies considerably from mill to mill, but is usually 2.5 to 4.5 kg/metric ton (5 to 9 lb/ton). Benefits include:
Improved tensile strength
Improved tear resistance, brought about by reduction of refining made possible by tensile improvement
No adverse effect on porosity
Higher production speeds
Kraft Linerboard
This industry was among the earliest users of guar and locust bean gum and remains so due to the introduction of newer high-speed, high-production paper machines. Guar and locust bean gum products have proved to be the most reliable and effective materials used to improve the Mullen test on this grade of board. Addition rates of 1 to 3 kg/metric ton (2 to 6 lb/ton) are normal in order to accomplish:
Higher speed at equivalent Mullen due to less need for refining, higher freeness, and thus, better drainage
Higher Mullen at reduced basis weights
More uniform Mullen values between top and wire sides
Optimum balance of refining, drainage, drying rates, and Mullen tests in 31.4-kg (69-lb) and heavier-weight boards.
Recycled Linerboard
Galactomannans are almost universally used by producers of this grade of paper, largely because of the use of reclaimed paper and board used in the pulp furnish of this grade. Gums provide the necessary upgrading of quality needed in the finished product. The need for guar and locust bean gum is particularly great in paper mills employing high-temperature, high-pressure dispersion units, but in all cases, gums provide these needed benefits at addition rates of 3 to 6 kg/metric ton (6 to 12 lb/ton). Benefits include:
Higher Mullen
Lower basis weight
Higher production speeds
More economical pulp furnish through use of more recycled paper
Improved finish
Corrugating Medium
Almost all medium made from recycled stock requires an additive to meet their strength tests. Galactomannans are commonly used additives.
The addition rate normally varies from 3 to 6 kg/metric ton (6 to 12 lb/ton). The benefits include:
Higher concorra
Higher speed
Better crush resistance in the finished container
Boxboard
Depending on the individual mill's conditions for stock preparation, specific products are recommended for addition to either beaters or hydropulpers. Usually mills making these grades prefer a product designed for dry addition to the stock at addition rates of 3 to 6 kg/metric ton (6 to 12 lb/ton) of liner stock. Ordinarily no gum is used in the filler portion. The resultant production or product benefits include:
Improved ply bonding
Increased board stiffness
Better formation of top liner
Better bonding strengths on coated grades
Offset News Stock
Paper mills have been able to realize through the use of galactomannans marked benefits in the production of stock for continuous web printing of newsprint at a use level of 1 to 1.5 kg/metric ton (2 to 3 lb/ton). Benefits have included:
Reduction of linting and dusting during paper manufacture
Higher pick values
Less build-up in printing on offset press blankets, permitting more impressions between cleanups.
White Papers
Guar and locust bean gum are used in a wide variety of white papers at addition rates of 1.5 to 4 kg/metric ton (3 to 8 lb/ton). By increasing sheet strength, it is possible to reduce the size concentration at the size press, with resultant improvement in tear, opacity, and calendering.
Gums used in high hardwood furnishes reduce surface picking, improve bonding of vessel segments, and increase fold.
Guar or locust bean gum is used in neutral or alkaline furnishes to improve the retention of calcium carbonate.
Galactomannans are added dry to the beater to reduce the refining time required to develop strength characteristics of rag content paper, particularly banknote.
These products are also very effective in decreasing two-sidedness and thus reducing the tendency of papers to curl.
Where formation is uppermost, gums are used to deflocculate the fiber bundles, closing up the sheet and markedly improving the appearance.
Mining
Guar gum is used as a flocculant to perform liquid-solid separations by means of filtration, settling, and clarification. As a typical filtration illustration, consider the acid leaching of a uranium-bearing siliceous are.
After crushing and grinding to 65% minus 200 mesh, the ore is leached at 55 to 60% solids with sulfuric acid and manganese dioxide at ambient temperature to extract the uranium as a uranyl sulfate complex anion. Some iron and silica also dissolve in the lixiviant, while the bulk of the silicates remain as residue. The pH of the leached slurry is less than 1 and the free acid content is 5 to 15 g/L.
The leached slurry is then distributed to a number of rotary vacuum drum filters using nylon or canvas duck media. Guar gum is added as a 0.1% solution to the leached slurry en route to the filter after hydrating for at least one hour at ambient temperature at a dosage of 0.05 to 0.1 kg/metric ton (0.1 to 0.2 lb/ton) of dry residue solids. This causes the fine residue particles to flocculate by bridging, whence a permeable cake is formed on the filters. The filtrate containing the bulk of the uranium is pumped to the uranium recovery circuit.
The residue from the primary filter is discharged onto a conveyor and dumped into a repulping tank with recycle filtrate from the secondary filter, thereby reducing the concentration of the uranium trapped by the residue. More guar gum is added to the repulped residue as it goes the secondary filter at a dosage of about 0.025 kg/metric ton (0.05 lb/ton). This causes the fine particles to reflocculate by bridging, whence a cake is formed on the secondary filter. Barren wash water is added to the top of the secondary filter to remove most of the entrapped uranium. Part of the secondary filtrate is recycled to the leach and part is used for repulping. The residue cake is conveyed to a tailing dump or goes to pyrite flotation.
A typical settling/clarification illustration follows the filtration example, except that a series of 5 to 6 thickeners are used in countercurrent decantation (C.C.D.) fashion, instead of filters.
After leaching with sulfuric acid and manganese dioxide or sodium chlorate, the leached slurry passes to the launder of a thickener, where it is diluted with return liquor from the next thickener in the C.C.D. series. Guar gum is added as a less than 0.05% solution (having been diluted from 0.5% with barren recycle liquor) at a series of three points spaced about 3 m (10 ft) from the thickener well at a dosage of 0.05 to 0.1 kg/metric ton (0.1 to 0.2 lb/ton) of dry solids. The overflow of the first thickener goes to metal recovery if the solution is clear. If not, some cationic guar gum is added to this solution prior to filtration on a diatomaceous earth filter to remove the fine colloidal silica. Another device is to pass this solution to which cationic guar has been added to a large settling tank for clarification prior to metal recovery.
The residue is removed from the first thickener by a diaphragm or centrifugal pump which causes some degradation of floc, and is pumped to the next thickener in the C.C.D. series. Guar gum is added in a similar manner as the first thickener but at a dosage of 0.025 to 0.05 kg/metric ton (0.05 to 0.10 lb/ton) to refloc the residue. The process is repeated with residue passing from the last thickener and pumped to tailing disposal. Fresh water or barrens are added to the last thickener to compensate for the rich uranium-bearing liquor removed from the first thickener.
Guar gum is used as a talc depressant in mineral flotation operations. As an illustration of a typical application, consider the flotation of pentlandite (Ni-Fe-sulfide) from a high-talc ore containing chalcopyrite, pyrrhotite, pyrite, serpentine, and biotite.
After crushing and grinding to a 90% minus 325 mesh a nickel-pyrrhotite concentrate is removed magnetically, followed by a treatment of the nonmagnetic fraction by flotation.
Flotation feed is diluted to 25% solids at a natural pH of 8.5 to 9.0. Guar gum is added at 0.2 to 0.3 kg/metric ton (0.4 to 0.6 lb/ton) to depress talc. The gum is added as a 0.5% solution hydrating at room temperature for 30 min. This is followed by 0.65 to 0.75 kg/metric ton (1.3 to 1.5 lb/ton) sodium ethyl xanthate as a collector and triethoxybutane as a frother. Rougher concentrate is removed with a total float time of 5 min.
Rougher tails is scavenged for 9 min after the addition of 0.05 to 0.075 kg/metric ton (0.1 to 0.15 lb/ton) guar gum and 0.3 to 0.35 kg/metric ton (0.6 to 0.7 lb/ton)sodium ethyl xanthate. Subsequently, the rougher and scavenger concentrates are combined and floated in the cleaners to produce a final concentrate and a middling recycle. No additional guar gum is used in the cleaners, but 0.15 to 0.2 kg/metric ton (0.3 to 0.4 lb/ton) of sodium ethyl xanthate and triethylbutane are added for a float time of 6 min.
The final concentrate assays 12 to 15% Ni, and the final tails assays 0.2 to 0.4% Ni.
In summary, guar and guar derivatives are used at very low concentrations below the level at which they thicken water. They are used as reagents which bond to hydrated mineral surfaces. In their application as depressants in base metal flotation, they function as agents to block the adsorpation of other reagents on talc and gangue surfaces. In flocculation, guar and guar derivatives adsorb on hydrated mineral surfaces by hydrogen bonding, and cause agglomeration by bridging.
INDUSTRIES USING GUAR GUM
Oil and Gas
Guar gum and guar derivatives are used in the fracturing of oil and gas wells because of their ability to thicken water efficiently at low concentration. They carry the sand or propping agent needed to keep the fracture from closing when the pressure is released. They are reliable polymers that will hydrate in field waters under many conditions.
Explosives
Guar gum and guar derivatives are used in the explosives industry because of their ability to efficiently thicken the nitrate salt solutions which are the basic components of slurry explosive formulations. The gums are readily crosslinked to form stable water-resistant gels.
Food
Guar gum is used in the food industry for its ability to bond and immobilize large amounts of water, thereby contributing to viscosity, inhibiting ice crystal formation in frozen products, modifying product texture, and stabilizing product consistency to changes in temperature. An illustration of the use of guar gum can be found in the manufacture of ice cream where small amounts of gum promote smooth chewy texture, inhibit ice crystal formation caused by heat shock, and impart slow meltdown qualities to the product.
Paper
In the paper-making process, guar gum adsorbs on hydrated cellulosic surfaces. It is a wet-end additive that promotes dry strength, improves sheet formation, and makes manufacturing easier and faster.
Textile
Guar and guar derivatives thicken the dye baths that are used in the printing and dyeing of fibers, fabrics, and carpets. The gums control the rheological characteristics of the dye formulations and permit complex multiple dye patterns that are sharp, bright, and controlled as to penetration.
Mining
In this industry, guar gum is used principally as a flocculant to produce a liquid-solid separation by filtration, settling, and clarification of mineral slurries. The property used is the ability of the gum to adsorb on the hydrated mineral particles by hydrogen bonding followed by agglomeration as a result of bridging.
Guar gum is also used in flotation to recover base metals. Guar gum acts as a depressant for talc or insoluble gangue minerals mined along with the valuable minerals.
FORMULATIONS
Ice Cream
10.0% |
Butterfat |
12.0% |
Milk, nonfat |
11.0% |
Cane sugar |
5.0% |
Corn syrup solids (42DE) |
0.3% |
Stabilizer/emulsifier |
38.3% |
Total solids |
Ice Milk
3.5% |
Butterfat |
12.0% |
Milk solids, nonfat |
11.0% |
Cane sugar |
8.0% |
Corn syrup solids(42DE) |
0.45% |
Stabilizer/emulsifier |
34.95% |
Total solids |
Sherbet
1.0% |
Butterfat |
3.0% |
Milk solids, nonfat |
20.0% |
Cane sugar |
8.0% |
Corn syrup solids (42DE) |
0.25% |
Stabilizer |
32.25% |
Total solids |
Sour Cream
18.0% |
Butterfat |
9.0% |
Milk solids, nonfat |
0.4% |
Stabilizer |
27.4% |
Total solids |
Buttermilk
1.0% |
Butterfat |
10.0% |
Milk solids, nonfat |
0.4% |
Stabilizer |
11.4% |
Total solids |
Yogurt
1.0% |
Butterfat |
12.0% |
Milk solids, nonfat |
0.8% |
Stabilizer |
13.8% |
Total solids |
Instant Imitation Bakery Jelly
30.00% |
Modified food starch |
0.50% |
Guar gum |
1.30% |
Sodium hexametaphosphate |
1.60% |
Dicalcium phosphate |
8.20% |
Adipic acid |
0.30% |
Raspberry flavor |
0.25% |
Raspberry Shade |
0.01% |
Purple Grade Shade |
0.70% |
Potassium sorbate |
57.14% |
Sodium benzoate |
100.00% |
Total |
Whipping Composition for Frozen Deserts
Parts by Weight |
|
50-70 |
Sucrose |
3-11 |
Modified food starch |
3-6 |
Gelatin (200 Bloom) |
0.5-1.5 |
Soy protein (degraded) |
1.0-1.5 |
Organic food acid |
0.1-0.5 |
Sodium hexametaphosphate |
0.2-0.6 |
Guar gum |
65.0 |
Fructose |
10.5 |
Modified food starch |
4.3 |
Gelatin (200 Bloom) |
1.0 |
Soy protein |
0.6 |
Flavor |
1.2 |
Citric acid |
0.25 |
Salt |
0.2 |
Sodium hexametaphosphate |
1.5 |
Color |
0.2 |
Guar gum |