PAINT FORMULATION
Paint formulation is the art of scientifically compounding properly selected raw materials for efficient manufacture of a competitive product that satisfactorily meets performance requirements.
Several terms are used in this definition of paint formulation and each term should be analyzed individually to give a better insight into the complexities of formulation.
ART
Art as the term is used here means a skill acquired by experience, study and observation, with emphasis on experience. Knowledge of the performance of the raw materials under the given conditions and in relation ship to each other is essential. This knowledge is largely dependent on experience. Many good formulators have had no formal technical training but develop excellent products based on years of practical experience. There are no precise scientific principles to apply that would insure a good formulation. Experience is an indispensable factor to the art.
SCIENCE
Though formulation is not a precise science, still scientific principles do apply. Several facets of paint formulation lend themselves to chemical and mathematical techniques. Pigment volume concentration is one such important approach. It will be discussed in some detail later in this chapter. With today's more sophisticated coatings such as epoxies, stoichiometric equivalents can be calculated to achieve proper balance between the resin and converter used to get maximum reactivity and eliminate trial-and-error methods. With the rapidly advancing technology of new vehicles and other raw materials, the scientific approach is gaining daily in importance.
RAW MATERIALS
The chemical industry is constantly introducing new compounds designed specifically or potentially for use in the paint industry. The alert formulator must keep abreast of these developments. He must know their properties as well as those of established materials. Proper selection of raw materials is essential. Small variations in properties between two otherwise comparable materials can mean the difference between a good or a poor finish. For example, two titanium dioxides may be identical in hiding power, whiteness, tinting strength and oil absorption, but can still result in vastly different performance. One of these may be surface treated to give it chalk resistance and tint retention and, hence, will produce an excellent exterior enamel. The other will chalk, lose its cleanness of tint and show rapid erosion. Knowledge of these small but important differences cannot be overemphasized for sound formulation.
MANUFACTURE
Efficient manufacture is always an important consideration in proper formulation. High-speed dispersion equipment, sand mills, attritors and other modern dispersing machinery are rapidly replacing the older roller, ball and pebble mills. This gives the formulator additional factors to consider: Particle size and particle size distribution of the pigment and the equipment to be used for dispersion now become problems for the formulator.
COST
The need for a competitive product is almost self-explanatory. If a product is over formulated, i.e., too good for its intended use, it may cost too much and no sales will result. Conversely, if it does not perform well, it will not be repurchased.
PERFORMANCE
With all these elements affecting the development of a good formulation, it becomes obvious that there is no unique answer for a specific formulation problem but rather that several equally good formulations can evolve. The only real criterion for a formulation is its performance.
For a proper start, these should be a clear definition of what is expected of the projected formulation. With these objectives defined, the selection of raw materials to achieve these objectives can begin. Frequently, a compromise may be necessary. Thorough knowledge of the characteristics of the ingredients and their interrelationship is necessary for a judicious selection.
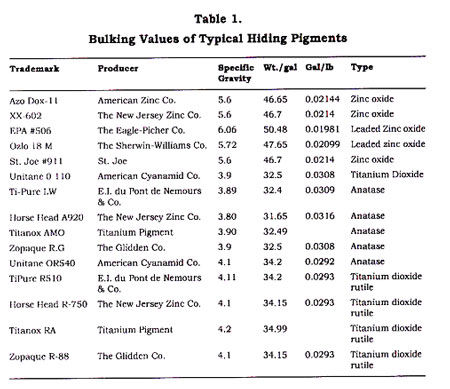
PRINCIPLES
The basic prerequisite for good formulation is a broad knowledge of the properties of the raw materials used in coatings. Also essential for a good formulation is a full awareness of the limitations of the raw materials to be used, their interrelationship with the other materials employed in the formula and, of course, the economics of their use.
Many factors, in addition to the basic ingredients, must be considered for a good formulation. These must be clearly defined before the development of a formulation is even attempted. These factors are determined by the anticipated end use of the proposed product. This is often overlooked and can result in much unnecessary laboratory work. The performance requirements, application properties, drying characteristics, color, gloss, hiding, production facilities, availability of raw materials, and selling costs are some of the factors that must be considered before development is begun.
With these requirements carefully outlined, selection of the proper raw materials based on a knowledge of their performance can be made, and the coating can be formulated to meet the stated objectives. Obviously this cannot be learned from a book but is dependent largely on a knowledge of the raw materials and the necessary experience to formulate a good competitive product.
Although emphasis is placed on the necessity of thorough knowledge of raw materials, there are some basic mechanics common to all formulations.
If it is assumed that the proper selection of raw materials has been made the performance characteristics of these materials in a given formulation are significantly controlled by the relationship of pigment and vehicle, specifically their respective volumes. The pigment-vehicle volume relationship will determine gloss, drying, stain removal, brushing flow, boldout, viscosity and other properties.
PIGMENT - VOLUME CONCENTRATION
This relationship is known as the pigment volume concentration (PVC) or simply pigment volume (PV). It is a percentage expressed as a number and represents the pigment volume divided by the sum of the pigment volume and the vehicle solids volume, multiplied by 100. Thus,
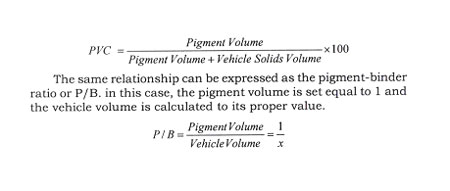
Critical Pigment Volume Concentration.
Still another concept of this relationship is the critical pigment volume concentration (CPVC). This is the specific PVC at which the vehicle demand of the pigment is precisely satisfied; i.e., there are no voids among the pigment particles. There is no excess vehicle present. This concentration is critical because above or below this value the properties of a formulation change dramatically.
In the pigment volume relationship, the formulator has a tool by which can change the scrubbability, enamel holdout, stain removal, dry hiding, gloss and other properties by varying the PVC. As defined before, the CPVC is the specific PVC at which pigment is completely surrounded by the vehicle with no excess vehicle left and no pigment voids. If additional vehicle is added, free vehicle is immediately available to enhance the gloss, scrubbability, etc.
As a specific example, if two given latices are compared in a given formulation, one may have a CPVC higher than the other. The higher CPVC formulation would predictably have better stain and scrubbability characteristics than the lower. If more pigment were added to the latter formulation to raise its CPVC, this would yield properties comparable to those of the first latex. Since pigment usually bulks at lower cost, comparable properties would result at a lower total cost.
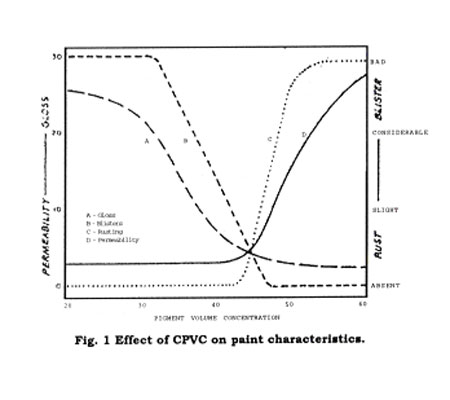
It is quite apparent now that the pigment volume is important. Exactly low is pigment volume or bulk determined? Bulk simply means the volume occupied by a given weight of pigment. For pigments, it can be calculated by multiplying the specific gravity by 8.33, the weight of a gallon of water (specific gravity = 1.0). Thus, if a pigment has a specific gravity of 1.5, its bulk will be
Bulk = 1.5 x 8.33 = 12.495 lb/gal
or if expressed as the reciprocal
1/12.495=.08 gal/lb
This simply means that every 12.495 pounds of this pigment used in a formulation will yield 1 gallon, or for every pound used, .08 gallon results.
These values are usually expressed as bulk per 100 pounds for ready comparison with the bulk of other pigments. Thus,
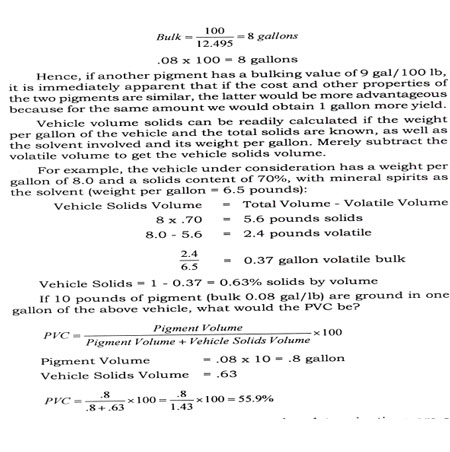
Critical pigment volume concentration determinations are a bit more complex and in a routine formulation are seldom calculated precisely. Usually a series of coatings at various levels or ladders of PVC are made. An enamel holdout test is run, and the approximate CPVC is established. Enamel holdout is a simple test and is exactly what the name indicates. The coatings under consideration are used as a prime cost and the enamel is applied over it. The concentrations between which the gloss or holdout changes markedly would be the approximate CPVC.
For a detailed discussion of CPVC, the reader is referred to the original work by Asbeck and Van Loo and their subsequent refinement, and also to the work reported by the New England Production Club.
Since the knowledge of raw materials has been stressed, we should now consider how their properties can affect the coating which is being formulated.
PIGMENTS
Prime pigments, i.e., those which provide the hiding or color, are of course essential because of their opacity or hiding power. The selection of a pigment for exterior application would be dictated by its durability. Will it chalk or not? How much will be required to get the proper hiding? For colored pigments, the lightfastness must be considered. From a viscosity standpoint, the oil or vehicle demand must be known. This property could affect the brushing, as well as leveling and gloss. The possible reactivity of the pigment with the proposed vehicle and its effect on package stability are important. Particle size and distribution may have an effect on the type of production equipment to be used in making the product.
In general, the same factors must be considered for the inert pigments. Here, these properties contribute to hardness, mildew resistance, stain removal, viscosity and control of gloss, in fact the same as for the prime pigment selection with exception of hiding power.
VEHICLE
The nature of the vehicle will to a large extent determine the performance of the coating. The vehicle must be selected with continuous awareness of the requirements of the product listed in the original request. In selecting the best vehicle, the following factors must be considered: whether it will be used inside or outside, its own color particularly in whites, its color retention, oil length, drying characteristics, reactivity with the proposed pigments, viscosity, the solvent present and the driers needed. Again there is no easy route to a quick selection of a vehicle except thorough knowledge and experience in its use.
SOLVENTS AND DRIERS
Although solvents are an integral part of most vehicles, additional solvents are frequently added to the formulation to adjust the viscosity, brushing or spraying characteristics. Solvent strength, odor, color, flash point, evaporation time, flash off point and toxicity must all be considered to obtain the desired balance of properties. With driers, the proper combinations of top- and through-dry must be evaluated.
FORMULATION EXAMPLE
The following is an example of the calculations required for the formulation of a white house paint to give the desired characteristics. Heatbodied linseed oil is chosen as the vehicle. The pigment is made up of titanium dioxide, leaded zinc oxide and talc. The principal hiding pigment is titanium dioxide and the proper balance is made between anatase (chalking) and rutile (nonchalking). The leaded zinc oxide is included to give mildew resistance, and the talc prevents settling and reinforces the film, thereby aiding resistance to chalking.
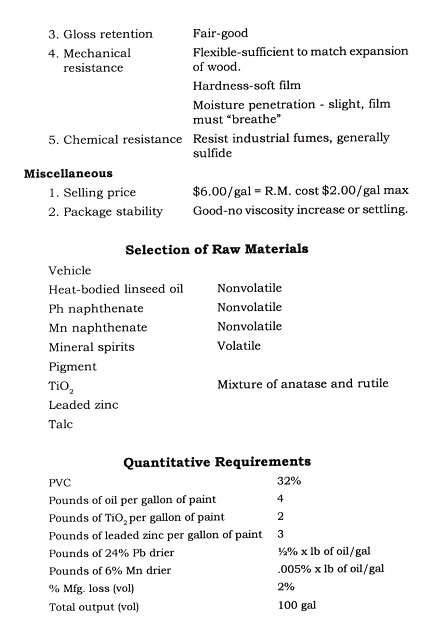
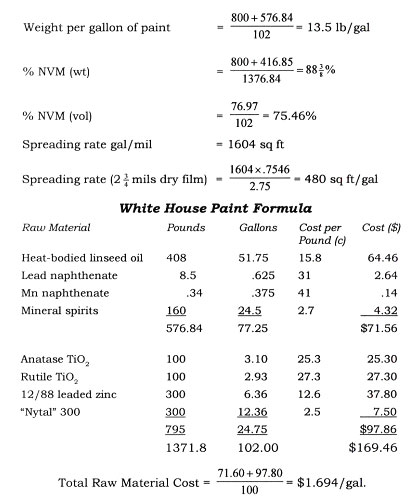
COMPUTER
More sophisticated techniques are gradually being introduced into paint formulation. For example, instead of many random experiments to establish the effect of a given set of variables, statistically designed experiments are used. By defining the limits of the variables under consideration and designing the experiments statistically to fit these variables, many needless experiments are eliminated.
Computers find more and more applications in the daily routine of a formulator. Williams and Bacchetta describe one such program for paint formulation. From one set of input data the program is capable of producing complete formulation data for up to five PVC's at a preselected volumetric solids content. In addition, the computer will generate such data as weight per gallon, pounds and gallons of each ingredient per 100 gallon batch, raw materials cost per gallon, pigment/binder ratio (P/B), and other useful information that is most time consuming when done by hand.
Naturally computers are expensive and hence not readily available. However, computer programs are available even for a small-sized company at nominal costs by a time-shared, client access computer system. Briber describes the operation of such a system, and many paint problems can be solved by its use.
MANUFACTURING TECHNOLOGY
1. PROCESS TECHNOLOGY
1.1 Paint Manufacture
The manufacturing of paint products depends just as much on proper manufacturing technique and good equipment as on good formulation and good raw materials.
Paint manufacturing is the process of mixing pigments with a suitable vehicle and grinding to a satisfactory fineness, colour and consistency. The equipment necessary to accomplish this is relatively simple and has been improved with the progress of the years to reduce labour and operating costs and to do a better technical job. Though the basic process has remained unchanged considerable advancement has taken place for improvement in respect of efficiency of various operations, optimisation in production cost, pollution control, etc.
A paint consist of three main components; the binder, the pigment, the solvent and few additives of various kinds such as plasticizers, driers, melting agents, flatting agents and emulsifiers.
The various operations needed to mix paints are completely physical. These unit operations are shown in proper sequence in the flow chart in Fig. A-1.
A standard paint manufacturer uses a three or four storey building where liquids are stored in tanks on the top floor and pigments are stored on the floor below. The production then proceeds by gravity to mixing, grinding, filling and storage of finished products on the floors below. Chemical conversions are involved in the manufacture of the constituents of paints as well as in the drying of the film. First step is the weighing, assembling and mixing of the pigments and vehicles. Proper mixing reduces the grinding operation as the pigments are partially wetted and some of the agglomerates broken up by the shearing action that is developed. Some easy wetting pigments can be dispersed so that no further grinding is necessary using a heavy duty dispersion mixer. The types of pigments and vehicles are dominant in the choice of equipment used.
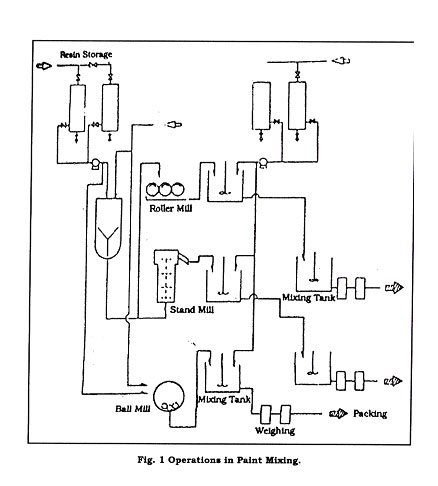
After mixing the paint is transferred to the next lower floor where it is thinned and tinted in agitated tanks. The liquid paint is drained into a transfer tank or directly into the hopper of the filling machine on the floor below. Centrifuges, screens or pressure filters are used to remove non dispersed pigments.
1.2 Powder Coating Manufacture
Compared to other powders, where the ingredients are mixed and dry ground in a mixer/blender and the finished powder is a blend of discrete ingredients, the powder paints are manufactured by melt mix process which involves the following operations. Fig. A-2 shows the manufacturing process flow sequence.
i) Premix and Extrusion
Raw materials are measured, roughly blended together and fed into a shearing and mixing extruder at temperatures greater than the melting point of the polymer constituents.
ii) Cooling
The extrudate from the extruder is fed between pinch rollers from where it emerges as a flat ribbon. This is chilled before substantial chemical cross linking takes place within the mix.
iii) Flaking
The ribbon is fed into a crusher to reduce it to flake form.
iv) Milling & Sieving
The flakes are reduced to a powder form in an impact mill. Each particle contains the entire formulation of the powder in its proper proportion. The milled powder is then air classified to make saleable product with proper particle size distribution.
1.3 Resin Manufacture
In the Paint manufacturing process, preparation of resins is one of the most critical operations. The detailed resin manufacturing process is discussed below:
Resins are one of the main inputs in the paint system. The resins are classified as synthetic or natural resins. The flow chart Fig. A-3 shows the production stages in resin manufacture.
The main equipments of resin plant are as follows:
- Reaction vessel or resin kettle
- Condensor
- Filter
- Thinning vessel.
The reaction vessel is the most critical part of the resin plant. The main process characteristics of resin kettles are reaction temperatures, overall endothermic effect of the reaction and nature of reaction substances.
The resin plants are further classified based on the source of heating i.e., direct heating or indirect heating through heat transfer fluids.
In direct heating kettles, it is difficult to control temperatures. In indirect heating the choice of heating media depends on the reaction temperature.
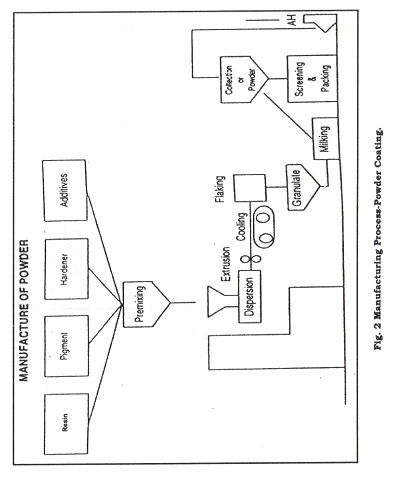
Steam is used where heating upto 200°C is required. For reaction temperatures higher than 200°C different heating systems like thermic fluid, electrical heating, induction heating, etc., are used.
2. EQUIPMENTS
The grinding media can be classified mainly into 3 groups:
- Shearing types
- Smashing or impact types
- The hybrid types
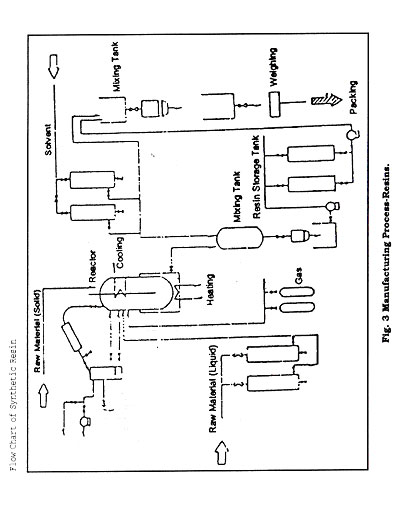
The various types of grinding mills used in Industry are:
i) Ball & Pebble Mills
These mills consists of steel cylinder mounted horizontally and rotated about their axis. Ball mills are steel lined and contains steel ball as grinding medium. Pebble mills use ceramic lining and steatite balls as grinding media.
ii) Sealed Horizontal Sand Mill
The Sealed Horizontal Sand Mill is a cylinder of various sizes filled with leads. The leads are agitated by horizontal motor driven shaft with metal disc spaced at intervals. The batch is usually primed through the mill at a speed which will produce the required fineness of dispersion.
iii) Edge Runner Mill
It is an efficient paste mixture and has a definite grinding action. This machine has one or two heavy rolls attached to a vertical shaft which rotates on a flat grinding surface.
iv) Triple Roll Mill
The triple roll mill is used for grinding pastes, stiff paints and putties.
A roller mill generally consists of three rollers which develop shearing stresses on a thin film of high consistency paste by virtue of the differential speeds of the rollers between which the paste in forced. Chilled hollow cast iron roll are used as rollers
.
v) Sigma Kneader Mixer
A high consistency pigment binder paste is subjected to mechanical break down by two inter meshing blades and the shearing action breaks down the agglomerates allowing melting. It is suitable for preparing pastes and high viscous substances.
It is available with heating and cooling system for pressurised and vacuum operations, with filling arrangement.
vi) Sand Mill
Sand mill is being widely used in paint industry. It permits dispersion on a continuous basis. The medium of grinding is spherical particles of quartz and with size/mm dia. Velocity difference in adjacent layers is developed due to motion of impeller and it imparts shearing action. The violent agitation of and induced by the agitator blade & effect shearing of pigment particles. The principle of dispersion is shown in Fig. 4. The sand mill consists of water cooled cylinder to a pump is attached which pumps the feed and feed is recycled for uniform grinding.
vii) Attritor Mill
This is used in most of the paint industries. In this mill pigment agglomerates are broken down by imparting them a high velocity by means of the rotation of specially designed motor blade in an open container.
viii) Mixers
The consistency of the material is of great importance while considering a mixer depending on materials viscosity.
Mixers are classified in two ways and further divided into three groups each.
A. Speed:
- High Speed
- Medium Speed
- Low Speed
B. Performance:
- Simple Mixing
- Mixing as well as grinding
- Mix the raw material to final product
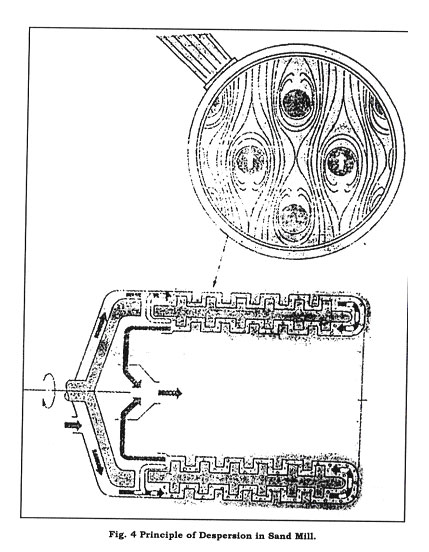
a) Dispersor
It contains a movable mixing system with a rotor stator system with wall scrappers. Batch size varies from 1 liter to 1500 liters for mixtures of solids and fluids of different viscosity. It has a variable agitator speed. The rotor stator system is designed in such a way that it disperse the pigments uniformly.
b) Planetary Mixers
Double planetary mixers use two lifting columns. It can have different types of mixing arms:
- Shearing blade mixing arm
- Hybrid mixing arm
- Three armed kneading tool
c) Cowels Dissolver
It is a medium to high speed mixer. This mixer is suitable for low viscous materials. The optimum action in the cowels dissolver is a combination of rotary and radical flow.
d) High Speed Disc Dispersor
These are simple quick and the least expensive for easy to disperse pigments in conventional vehicles. The main limitation is their inability to disperse hard or tough agglomerates. The equipment consists essentially of a circular raw blade of impeller mounted on a shaft rotating at high speed which is vertically centered in an upright cylindrical tank.
3. LABORATORY EQUIPMENT
The various laboratory equipments used for quality control are:
i) Flow Cups
For many applications it is not necessary to know the absolute viscosity of a paint or varnish. A parameter permitting a relative classification and estimation is considered sufficient. The efflux time measured in seconds, is such a reliable parameter. It is determined using flow cups of various designs.
ii) Gloss Reflectometer
The gloss reflectometer is designed to measure specular gloss, reflection gaze and mirror reflection of brightened metal surfaces. The simultaneous measurement of gloss and reflection gaze allows a confident and objective evaluation of surface quality.
iii) Cross Cut tester
The cross-cut test is a method for evaluating the adhesion of single or multicoat systems.
iv) Chequer board & P-Fund Cryptometer
These are used to determine wet opacity of the paints.
v) Colour Matching Computer
The system contains a software with following features:
- Measure & match any colour sample
- Retint leftover and mistinted paint
- Stores formulae
The software is PC compatible, it uses a color spectrophotometer, designed for measurement accuracy and reliability of the paint.
vi) Weather-o-Meter
4. QUALITY CONTROL
The Quality Control is of prime importance in paint manufacturing. Strict quality control is required not only for finished products but also for the raw materials used. The inconsistency in the quality of raw materials is one of the main reasons for poor quality of finished product. In the developed countries, the quality control is more stringent than in India. The raw material suppliers have adequate quality control equipment to meet the requirements of paint manufacturers. While in India, except a few major raw material suppliers, the expertise and resources to provide quality comparable to international standards is lacking. This leads to inconsistency in the quality of raw materials which in turn affects the quality of paints. The large paint manufacturers in India have modern testing equipments and expertise to deliver quality products. Certain manufacturers such as Asian Paints, Goodlass Nerolac, Garware, etc. have taken adequate steps to maintain quality of the end product by investing in personnel, laboratory equipment and manufacturing process. The small sector, especially the tiny sector, lacks resources of large manufacturers to provide for systems and sophisticated laboratory equipment for stringent quality control. Hence the tiny sector mainly produces low technology paints such as primers, putty etc.
5. AUTOMATION
Paint production involves hundred of formulations, over a thousand different raw materials, divergent batch volumes etc. The major cost of paint manufacturing is on account of raw materials followed by labour. As there are number of expensive raw materials required for paint manufacture, any wastage of these would lead to increase in cost. Hence automation is considered to be a key factor today. Automation is commercially viable in a large plant with a continuous production of large batch sizes or a single product line.
The importance operations while considering automation are:
- Delivery of resin & solvent to the mixing vessel
- The addition of pigments & additives
- Premixing/Dispersion to the desired level
- Colour correction/Viscosity adjustments
- Filling, Packing and despatching.
Table A-1 shows the labour cost of different operations as % of total labour cost.
Table A-1
Labour Cost of Different Operations as Percentage of Total Labour Cost
| Work | % of Labour Cost |
i. |
Filling |
35-45 |
ii. |
Charging, Pre-mixing and dispersion |
20-30 |
iii. |
Colour & other adjustments |
15-25 |
The level of automation in Indian Industry is quite low and it is almost non-existent in the small sector.
THE MANUFACTURE OF SPIRIT VARNISHES
By the term "spirit varnishes" is meant varnishes which consist of a simple solution of resin in a solvent. Plasticisers may also be added. The preparation of these varnishes involves no laborious or complicated cooking process.
It is one of the simplest processes of the varnish factory, and because of this it has been assumed that no technical skill is necessary, and that almost any vessel capable of holding a liquid will do.
The type of varnish required, and the constituents involved, really govern the best type of plant to be used.
Among the spirit varnishes may be included, solutions of shellac or bleached shellac, soft manila, accroides, oxidized rosin, phenol- and urea- formaldehyde resins, and modified phenolic resins in industrial alcohol; and solutions of coumarone, damar, limed rosin, rosin and copal esters, modified phenolic, maleic and other synthetic resins in hydrocarbons.
The treatment of these varnishes during their production depends upon the chemical properties of the resins, the amount and form of the insoluble matter, and the viscosity of the final product.
Spirit Manila Varnishes
Under normal circumstance more spirit or soft manila is used in spirit varnishes on an industrial alcohol base than any other alcohol-soluble resin, with the possible exception of rosin.
Spirit manila is an acidic resin, having an acid value of the order of 140. It varies in hardness; some types are fairly hard and brittle, others are soft and sticky. Its solubility is likely to vary considerably. Some grades contain appreciable amounts of slimy, stringy material which is insoluble in alcohol. Several percent of dirt, consisting of mineral matter, bark, twigs, etc., is common. All these special features require careful consideration in designing the ideal plant.
The acidity of the resin indicates its reactivity and tendency to discoloration in contact with mild steel. Thus, large wooden mixers or churns are commonly employed. Some factories employ mild steel, ignoring its disadvantages, but stainless steel is the best choice. If desired, it permits other and more sensitive types of varnishes to be made in the same mixer.
The rate at which the resin dissolves depends upon the rate of movement of solvent past the individual lumps of resin, and the concentration of the solution. The design of suitable stirrers has been covered in the chapter devoted to mixing.
Few, if any, mixers now used have facilities for heating their contents, yet an increase of temperature of 20°-30°C. above room temperature has a great effect on rate of solution. Higher temperatures are not advisable because of the relatively low boiling point of alcohol. Low-pressure steam, therefore, serves admirably as a heating medium.
The removal of the large proportion of dirt present after the resin itself has dissolved constitutes one of the problems of this type of spirit varnish manufacture.
It is normally either run out of the mixer with the spirit varnish and roughly strained out before it enters the filter tank, or it is allowed to accumulate by settling in the mixer, which is then cleaned out later. Straining of large volumes of spirit varnish is a costly and tedious operation. Disposal of large amounts of accumulated dirt, wet with varnish, means that valuable occluded varnish finds its way to the refuse heap or the incinerator.
The most economical procedure to adopt for dirt treatment is to allow the dirt to settle when the first batch of varnish has been made. This need not occupy more than an hour or two, for settlement of all the dirt, including the finer particles, is not necessary. The subsequent filtration or centrifuging will deal effectively with these. The length of time required for settling can, however, be greatly curtailed if the varnish is maintained at a temperature above air temperature, for its viscosity is reduced in proportion to the temperature. This is another argument in favour of the adoption of a jacketed mixer.
After the dirt has settled sufficiently, the supernatant varnish can be run off, into a filter tank, for further treatment.
A further batch or two of varnish can be made in the same mixer, until the accumulated dirt is almost fouling the discharge cock for the varnish.
The discharge cock is located at a convenient position some distance above the bottom of the mixer.
As much varnish is removed by means of this cock as possible, and the mixer is then partly filled with new solvent. The stirrer is then run for a short time to allow the solvent to wash off as much varnish from the dirt as possible. After settling, the solvent containing the extracted varnish is withdrawn through the varnish cock. The remainder, below this level, is drained away through another cock in the base, care being taken to prevent too much dirt from passing through. The entrance to this cock is prevented from being blocked by a perforated disc. This in turn is kept clear by the movement of the bottom blades of the stirrer.
Since industrial alcohol is cheaper than spirit manila it is more economical to leave the insoluble dirt wet with a dilute solution of varnish than with varnish at normal concentration. Even if the alcohol and the resin were of equal value, the volume of the occluded liquid would be less after the thin solvent mixture had drained from it, than after the more viscous, undiluted varnish.
The washed dirt is removed manually through a large hand-hole at the bottom-side of the mixer.
The diluted varnish is sent to a temporary reservoir tank, from which it is returned to the mixer to be used as the solvent or part of the solvent for the next batch of varnish.
Many spirit varnishes are often coloured by the addition of soluble dyes, and these can be incorporated in the mixers, and dissolved at the same time as the resin. The application of heat also facilitates the dissolution of these dyes. Obviously, if dyed varnishes are made, special adjustments in plant will be necessary. It may be most convenient to reserve a mixer for each colour, if the quantities are sufficiently large.
From the mixer the varnish must be subjected to further cleansing. If it is to be pigmented, centrifuging is satisfactory. If, however, it is to be used as a clear lacquer, where brightness, clarity, and gloss of film are important, then filtration is nearly always essential.
A general arrangement of a plant for manufacturing spirit manila varnishes is shown in fig. 1.
If spirit manila varnishes of high viscosity are required, there are limits to the viscosity which can be handled economically in a mixer of the type described. It is not only a question of dissolving resin in an already viscous solution, but of removing dirt from this very viscous product. A heated mixer and a heated press will handle fairly viscous products, but the almost paste-like mixtures, used as adhesives, are beyond the scope of these plants.
The only really satisfactory way of producing such products is to make a varnish of normal viscosity first and then subject it to a distillation in a small plant afterwards. The distillate can be used as solvent for the next batch. Evaporation of varnish in open steam pans in order to attain a higher viscosity is wasteful and crude.
Shellac Varnishes
These varnishes can be made in the same plant as that used for the manila varnishes, with slight modifications.
Shellac is much more susceptible to discoloration than manila copal, and for this reason much greater care must be exercised in choosing materials for plant construction. No part of the equipment should be mild steel. Possibly the cheapest and most satisfactory mixer to use is a wooden one.
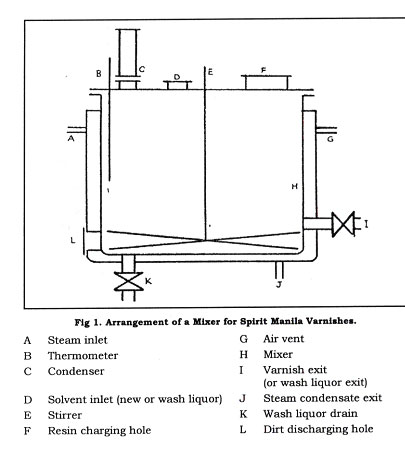
Ordinary shellac is sold in the form of flakes, unlike manila copal which may be received as lumps of practically any size. By reason of the softness of manila it is quite likely to cake into large agglomerates under warm storage conditions. Because shellac is available as small flakes, the area presented for its solution is large, and a well-designed stirrer will effect solution in a few hours without the application of heat. This is fortunate, for shellac is heat-sensitive and polymerises fairly readily. Where very viscous shellac solutions are required, it is not possible to prepare them by distilling off surplus solvent unless reduced pressure is used. In any case this procedure should be used only when more scientific ones cannot be adopted. It must be used for dirty resins like copal, but shellac being normally much cleaner, can be converted into a viscous product by using mixers employing intermeshing horizontal blades of the Beken type.
If it is necessary to clean thinner shellac solutions, this is best accomplished in a centrifuge. Shellac solutions can be filter-pressed, but a great deal of care is necessary to do this satisfactorily.
Accroides Varnishes
In most respects these resemble spirit manila varnishes. Accroides is possibly the dirtiest spirit soluble resin used, and any plant must take care of this peculiarity.
Accroides is also heat sensitive but not to such a marked degree as shellac. A steam jacketed mixer, employed skillfully, is an advantage.
Cleaning is best accomplished in a centrifuge, because it behaves like shellac in its ability to clog filter papers quickly.
Oxidised Rosin Varnishes
Although oxidised rosin is a high acidic resin, and as such has a tendency to attack metals under certain conditions, its natural colour is a dark reddish brown, and any further metallic discoloration is usually masked or unimportant. No one employs oxidised rosin in pale lacquers or delicate shade spirit enamels.
Mild steel equipment is quite satisfactory, for, although metallic corrosion occurs as evidenced by some colour change, its magnitude is of a relatively low order as measured by amount of metal dissolved. A mild steel mixer will last many years.
Oxidised rosin is not thermosetting, and the extent to which the mixer can be heated is limited only by the boiling point of the solvent present.
The resin is also very clean and solutions do not require any cleansing treatment.
Phenolic Resin Varnishes
These fall into two classes, those involving pure unmodified resins, and those involving the highly rosin modified types.
The former are both sensitive to heat and to darkening in contact with iron. The latter are affected by these conditions to a much diminished extent. Both are similar in that they do not need any special cleansing plant.
The pure phenolics are best treated as for shellac; the rosin modified resins can be treated as for spirit manila.
Urea-formaldehyde Resin Varnishes
These resins should not be encouraged into solution by the action of heat, and except for this the mixer as used for spirit manila varnishes is satisfactory. No provision need be made for dirt removal or special cleansing.
Hydrocarbon Base Varnishes
To accommodate all varnishes of this type stainless steel equipment is recommended.
Most of the resins in question, however, are neutral or nearly so, and the cheaper mild steel is quite satisfactory for these.
There are three ways of manufacturing these products. The first is by dissolving the resin in the solvent, by agitation of the solid and the liquid, either in the cold or at a slightly elevated temperature. The second is by melting the resin in a separate vessel and discharging it into the mixer containing solvent.
The first method gives somewhat paler products, but the second gives a greater output in a given time. The cost of heating is offset by the cost of agitating a large bulk of resin and solvent for several hours.
A compromise between the two methods is sometimes preferred, wherein the resin is dissolved by agitation in the solvent, at a temperature intermediate between the ordinary air temperature and the melting point of the resin.
None of the resins commonly used-coumarone, damar, ester gums, resinates, or modified phenolic or maleic resins, are heat sensitive.
Their solvents usually have much higher boiling points than industrial alcohol. Thus it is feasible to facilitate solution by raising temperature of the two components to 100°C. or more.
With the exception of damar, no special provision need be made for removing accumulated dirt from the mixer, or for cleaning the product.
Obviously the most economic way of making solutions of some of these resins is to send them directly to a mixer as soon as they are made, whilst they are still liquid and hot. No secondary heating is required and very pale varnishes are obtained.
This procedure is, of course, possible only when the varnish maker is processing his own resins.
THE MANUFACTURE OF PAINT REMOVERS
Paint removers can be divided into the following types: those based on aqueous alkaline mixtures; those which are clear solutions involving strong combinations of solvents often with suitable bodying agents; and those which contain waxes partly precipitated from a mixed solvent.
The first type are beyond the scope of this section, whilst the second type are simply prepared by dissolving a bodying agent in suitable solvents.
This short chapter is designed primarily to deal with the wax-containing removers.
The theory behind their formulation is that the solvent mixture used is a blend of wax-solvent and wax-precipitant. Both types of solvent are carefully chosen for their special solvent or softening properties on applied films.
The design of the plant will be governed in the first instance by the inflammability of the solvents used.
Common solvents which might be employed are acetone, methyl ethyl ketone, benzol, toluol, methyl alcohol, and ordinary industrial alcohol, to name but a few of the very inflammable low-boiling solvents in general use.
The mixer should, therefore, be totally enclosed and all motors for stirring gear or ventilation should be of fire-proof construction.
No great heat is required for the manufacture of these wax-base removers, and a steam jacket suffices. The only heat required is that to melt the wax in the first place, and very few waxes have melting points in excess of 100°C.
Again, the wax does not constitute a very high proportion of the finished product, and it is necessary only to melt this relatively small amount of wax in the lower half of the jacketed vessel. In other words, the steam jacket need not extend more than one-third of the total height of the vessel.
The melting of the wax can be facilitated by the action of a light stirrer, which also serves to agitate the mixture in the later stages of production.
The solvent, which is a solvent for the wax, is next admitted by means of a pipe through the cover. This can be of the largest cross-sectional area which is possible within reason, for this solvent can be admitted as quickly as the pipe will convey it, as soon as the wax has completely absorbed the first small amount of solvent.
To the clear cool solution of wax in solvent is added the wax-precipitant. This is added slowly with constant stirring, to cause the wax to precipitate uniformly, and ultimately as a thick homogeneous cream.
To obtain the best results it may be found necessary to cool the original wax solution, before admitting the precipitant, and a bank of cooling coils may be installed in the vessel.
The making vessel should have a large discharge valve at the bottom to permit the passage of the product which should be slightly thinner than a creamy consistency when warm. To facilitate filling the product is best discharged immediately into the containers in which it will be dispatched.
Neither the solvents nor the waxes present any corrosion problem, and a mild steel vessel with the ancillary equipment is quite suitable.
This is one vessel where no special opening for cleaning need be provided, for no dirt is likely to accumulate inside it.
A semi-continuous process can be divised if a separate premelting vessel is supplied for the wax. The molten wax can be delivered into the warm mixing vessel, at the same rate as the wax solvent. The rest of the wax solvent can then be added, followed by the precipitant. As soon as precipitation has been effected and the product cooled, it is discharged, more premelted wax is run in and the process is repeated.
It does not need much vision to see that the process can be taken one step further and made absolutely continuous. It is merely a question of admitting liquid wax, solvent and precipitant into a system at a predetermined rate.