Printing Ink Driers or Siccatives
NATURE OF INK DRIERS
A DRIER is a chemical additive which has the power of accelerating the drying time of a drying oil, and of many synthetic resin varnishes which dry by air curing, e.g. alkyds. A drier aids the drying of those oils which form a solid film of linoxyn when exposed to air by an oxidative polymerization process. No amount of drier will cause a mineral, lubricating, or spindle oil to dry. The driers have the properties of catalysts in that they accelerate the rate of a chemical reaction, which in drying oils is reacting with oxygen in the air. Apart from salicylic acid which has a mild siccative or drying action, the driers used are metallic compounds. The metallic concentration is the fundamental activator, and driers have been bought by assessing their merit as the number of units of metal per unit of cost. Some metals exert a more powerful drying influence than others. As metals are insoluble in drying oils, it is an oil soluble compound of the metal that must be used, and it is these soluble metal compounds which are termed driers.
GENERAL USE OF DRIERS
Driers are used in oil-based and synthetic-resin inks. They are employed to assist the drying of all letterpress, planographic, copperplate engraving, steel-plate engraving, and quickset inks. They are used in all gloss varnishes, overprinting varnishes, and tin-printing inks. They are fundamental constituents of many die-stamping inks, some oil-based silk-screen inks, most roller coatings, and roller-coating inks.
PASTE AND LIQUID DRIERS
Both paste and liquid driers are used in making printing inks. Paste driers consist of certain metal salts such as acetates, borates, or oxalates, finely ground in a drying oil, usually together with some inert filler such as barium sulphate. The dispersion of paste driers is generally improved by the addition of an aromatic or fatty acid which has a stabilizing and peptising action. Liquid driers are metallic soaps, e.g. linoleates, naphthenates, which are soluble in turpentine, white spirit and drying oils. The approximate order of the effectiveness of the metals is Cobalt, Manganese, Cerium, Lead, Chromium, Iron, Nickel, Uranium, Zinc, Platinum, Palladium, Calcium.
Cobalt driers are the linoleate, linolenate, naphthenate, xanthate, resinate and, for paste driers, the acetate and borate.
Lead driers are lead naphthenate, lead resinate, litharge, and red lead.
Lead paste driers may contain the acetate.
Manganese driers include manganese sesquioxide, manganese dioxide, the borate, resinate, linolenate, oxalate, linoleate, and naphthenate.
The borate is obtained as a precipitate by adding manganese sulphate solution to a hot solution of borax. The oxalate is made by adding a solution of sodium oxalate to a solution of soluble manganese salt. Manganese driers are usually highly coloured and are often claret shades.
The metallic 'octoates' are becoming popular as driers: these are the metal salts of 2-ethyl hexoic acid; this is a pure substance of low odour.
THEORY OF THE PROMOTION OF DRYING
Much more than the percentage metal content must be known to calculate the activity of a drier. Drier efficiency or activity depends upon the percentage metal in active form which is not accurately known, the degree of dispersion of the drier which is uncertain, and surface energy properties of the drier which cannot be computed. Drying also depends on the rates of diffusion of several different organic oxygen containing radicles in the exposed film. These diffusion rates must constantly change as the polymerization proceeds, as the film viscosity increases, and as the dispersion of these oxygen products in the film alter.
A metal that can form more than one oxide acts as a drier or oxygen carrier when dissolved in oil, providing that the lower valency state is stable. Exceptions to this are the mild driers calcium and aluminium, but their lack of drying power may be connected with lack of variable valency. An important aid to the effectiveness of a metal may well be its reducibility from a trivalent to a divalent state. Witness the greater drying power of trivalent cobalt, manganese, and cerium.
The acidic part of the soap, however, is in some way involved. Chlorides and nitrates are rarely used as driers, while acetates and borates are good driers. Lead stearate is ineffective compared with lead linoleate and linolenate. Lead tetraethyl dissolves in linseed oil, but at low or high concentration it is an inefficient drier. Livache showed that finely divided lead could act as a drier, rather indicating that the metal content of the drier must be readily available to the varnish. Active peroxides in a drying oil can render the metallic driers ineffective.
Driers can modify the nature of a drying oil into which they are introduced. Thus boiled oils containing pyrolusite and litharge driers give hard and brittle films, distinct from films of refined oils with the same driers at the same concentration. Again, manganese driers are useful with modified phenolics, while cobalt and lead are useful for alkyds, drying oils, maleics, and pure phenolics. Further, it is established that cobalt and manganese catalyse surface drying, while lead catalyses 'through' or 'lower drying'.
Certainly a direct correlation between the metal content and its drier activity cannot be maintained, unless proper account is taken of the percentage metal available in an active form which would depend upon the precise constitution which is not accurately known, and the degree of dispersion which is uncertain. A study of the surface energies of the driers would be necessary. The rates of diffusion of oxygen products in the drying film depend on the viscosity of the material, polymerization of the products, and the change in their dispersion in the film. Another fact to remember is that the activity of metals in such solutions is vastly different from what it is in aqueous solutions.
In fact, metallic driers are not normal catalysts, but promoters absorbing oxygen selectively on the surface, followed by chemical reaction. Again, the drying of some of these inks takes place in two stages: a thickening of the film, which keeps becoming more viscous, followed by a gel structure which keeps hardening. The constitution of the drier, the concentration of 'active' metal, the degree of dispersion of the drier, the rate at which oxygen can diffuse in the drying film, the extent of the colloidal nature of the ink, and the precise nature of the chemical drying are all inaccurately known factors affecting the problem of metallic soaps aiding drying. A few empirical rules can be stated, but no rational theory of how the drying is promoted can be given.
The fact that they are efficient aids to drying is firmly established. A film of refined linseed oil which dried in 110 hours was treated with different 'precipitated linoleate' driers individually. A concentration of 0.05 per cent cobalt metal so introduced caused the oil to dry in two hours; 0.08 per cent manganese cut the drying time to five hours; 0.5 per cent lead to seventeen hours, and 0.5 per cent iron to twenty-four hours.
METHODS OF PREPARATION OF LIQUID DRIERS
(1) By the reaction of inorganic metal compounds and vegetable oils.
Lead acetate and lead borate can be heated with drying oils. Red lead is heated with linseed oil above 240º C., and litharge is so heated at 220º C.
The mechanism of the reaction seems to be as follows: the litharge reacts with the free acid to form ester and water the ester is pyrolyzed to give acid, carbon dioxide, and water. The oxygen involved is obtained from the air. The drying oil is hydrolyzed by the water to give alcohol and free acid and these products react with litharge to give lead soaps and lead glyceroxide. The water evolved enables the reaction to continue. Litharge and lead linoleate yield a basic lead linoleate. The drier content is thus lead linoleate, basic lead linoleate, lead glyceroxide, and probably some dispersed litharge.
Rose pink cobalt hydrate reacts with linseed oil at 260ºC. to give a claret syrup. At the end point a drop of the medium removed should be clear when spotted on glass. Cobalt, manganese, and calcium hydroxides which have been freshly precipitated in the absence of air react with drying oils at 190º-200º C. to give pale driers.
(2) By the reaction of inorganic metal compounds and fatty acids to form 'fused driers'.
The acids normally used are L.O.F.A., tung oil fatty acid, rosin, hydrogenated rosin, polymerized rosin, naphthenic, and oleic acids. Such acids react with metallic oxides to yield soaps soluble in turpentine, white spirit, or naphtha. The so-called 'terebine' driers belong to this class. The products are the fused linoleates, tungates, naphthenates, resinates, and oleates. A somewhat lower temperature can be used than when reacting the oxides with the oils; L.O.F.A. and litharge are reacted at 150º C., but with manganese dioxide the temperature is 230º C. Fused resinates are made by reacting rosin with litharge at 200º C., with cobalt hydrate at 200º C., but with manganese dioxide at 240º C. Wool grease fatty acids react with the oxides of cobalt, lead, manganese, and zinc at 155º C. Driers can be made by heating the metallic oxides with coconut oil fatty acid and dissolving the soap formed in naphtha at 100 ºC. to give a clear solution. Metallic salts in aqueous solutions have been reacted with these fatty acids. The metal soaps have also been made in the presence of solvents, e.g. by using fatty acids dissolved in solvent.
(3) By the reaction of metal compounds with mixed drying oils and their fatty acids.
A well-known example is to prepare freshly precipitated, wet cobalt hydroxide in the absence of air, and convert it into a paste with linseed stand oil. The paste is heated at 95º C. with 50 per cent rosin in mineral oil.
(4) By the precipitation method. Metal compounds are reacted with the sodium, potassium, or ammonium salts of organic acids. Suitable metal compounds are the acetates, sulphates, nitrates and chlorides. Suitable acids used as their alkali salts are L.O.F.A., tung fatty acids, perilla fatty acids, stillingia fatty acids, wool grease fatty acids, rosin, naphthenic acid, oleic acid, tall oil, and 2-ethyl hexoic acid. The theoretical quantity of aqueous caustic soda, potash, or ammonia, is heated with the fatty acid. Alternatively, drying oils are saponified with caustic soda, the soap formed being boiled for an hour or more with efficient stirring. A floating tar of unsaponifiable matter may have to be removed by muslin straining. The hot, aqueous metallic salt solution is added to the boiling soap solution, until the mother liquor becomes neutral to litmus. The precipitated metal soap is slowly heated at 115º-l20º C. with stirring to remove all occluded water. Vacuum heating or suction filtration followed by drying at 40º C. have been used. The heating must be cautious and curtailed since metallic soaps tend to darken in colour and decompose. If skinning occurs there is loss of solubility.
Fluxes have often been added to the soap just before dehydration to keep it liquid. Plasticizers such as tricresyl phosphate, dibutyl phthalate, and benzyl benzoate, have been used. The metal soaps are more stable in aromatic hydrocarbons than in aliphatic hydrocarbons. Instability is characterized by semi-colloidal soap dispersions in highly viscous media which slowly gell and precipitate part of the soap during storage. Basic soaps are always present in these driers. The fusion method usually gives more stable driers, because the reaction is incomplete and leaves some free acid to have a peptising effect on solutions. Often stabilizing acid mixtures are specially added. Recommended mixtures are stearic, mandelic, and cinnamic acids; palmitic and benzoic acids; or hippuric and salicylic acids. The amount varies from 0.5 per cent benzoic acid to 7 per cent of high molecular weight acids. About 7 per cent palmitic acid is suitable for cobalt linoleate. Basic stabilizers have been used such as ethanolamines and diamines.
Sometimes dehydration of the drier is effected by solvent treatment and distillation. The bulk of water is decanted from the precipitated soap to which a solvent like white spirit or benzene is added. The solvent is distilled to leave the dried soap in solution. Precipitated soaps which are flocculant are alcohol washed. Another method of making these driers involves using organic solvent at the time of precipitation. Mineral spirit and xylene have been used.
(5) By reacting castor oil with metal compounds. The hydroxyl group in castor oil is replaced by metal by heating the oil with the metal or metal compound at 240ºC. The products are soluble in turpentine or white spirit at 100º C.
To make a solution of a drier it is usual to add the solvent - white spirit, turpentine, or naphtha - slowly with much stirring, and gently warm to 50º-100º C.
PROPERTIES OF LIQUID DRIERS
- Optimum concentration. Increasing the metal concentration improves drying systematically only up to a certain limit. The upper limit for refined linseed oil is lead 0.8 per cent, manganese 0.1 per cent, and cobalt 0.04 per cent. For tung oil the limits are lead 0.25 per cent, manganese 0.03 per cent, cobalt 0.02 per cent. The varnish itself can cause a difference and dry better with a specific catalyst. Zinc is better than manganese for some alkyds. Excess driers are not in any way helpful; it is the controlled use of driers which is important to the ink maker.
- Drying characteristics. Cobalt, manganese, and iron cause surface drying, while lead, cerium, and calcium promote 'through' or 'lower' drying; this may be connected with the effect of the drier on the surface tension of the varnish. Lead reduces the surface tension of linseed oil, but cobalt and manganese increase it.
- Mixed Driers. A combination of driers in often used to secure the best characteristics of all the driers present. The following mixture is popular and effective: lead; manganese; cobalt, in the ratios 5:1:1.
- Nature of Acid Radicle. This has a definite effect and has already been alluded to. The linoleates are the most popular, but the naphthenates are firmly established as useful driers and have many advantages. These are:
- Higher metal content and less drier is consequently added.
- They dissolve more readily and are more stable. Lead naphthenate is an exception.
- They skin less and are not so inflammable in storage.
- They have a reduced tendency to become poisoned driers.
Alchemy Ltd. manufacture a 12 per cent cobalt octoate drier and a colourless 32 per cent lead octoate drier which have the advantage of higher metallic concentration with solutions of only syrupy consistency. Renewed interest is being shown in rare metal octoate driers which contain cerium as these are only mid yellow in color. Zirconium octoate solutions are now readily available as 'cobalt drier catalysts'. The zirconium ensures that all the cobalt metal present is actively available in promoting drying instead of part remaining ineffective. Ink makers will always search for pale driers, although the ones available at present are weak even in high concentration because of the urgent need in some cases to keep down the colour of the varnishes. Obvious uses are gloss varnishes, very light-coloured inks, and cases where only mild drying action is required.
The 2-ethyl hexoates are perhaps even better driers than the naphthenates.
(5) The absorption of drier by pigment. Pigments with large specific surface areas show the greatest power of removing driers, e.g. carbon black, siennas, umbers, madder lake, zinc oxide. Trivalent metals are absorbed faster than when they are in the divalent state.
APPEARANCE OF THE DRIERS
Pure cobalt linoleate is a violet, viscous liquid. It is used diluted with linseed oil, L.O.F.A., or mineral oil; and is usually supplied at about 5 per cent metal concentration. Cobalt naphthenate is a solid, M.Pt. 130º C. In mineral oil cobalt naphthenate tends to thicken on storage and stabilizers are normally added, such as acids or butanol. Cobalt soaps give dark green solutions in turpentine.
Most manganese drier solutions are red. Precipitated manganese linoleate is orange, but the fused variety is a red-brown solid. Fused lead linoleate is a brown, cheesy solid. The white-spirit solutions are cloudy. Lead resinate is a solid, and lead naphthenate is orange with M.Pt. 100º C. The naphthenate gives a clear solution in white spirit. Lead driers must be used with caution because of their tendency to precipitate from solution. Calcium linoleate is a white powder, and calcium naphthenate is a viscous, straw-coloured liquid.
STANDARD SPECIFICATIONS
Paste driers must be smooth, homogeneous pastes which can be broken up into a smooth mixture when stirred well with four volumes of linseed oil and one volume of turpentine. The paste must consist of a mixture of drying agents and insert mineral matter, together with refined linseed oil. Not more than one-half of the mineral matter must be calcium compounds calculated as the sulphate. A representative sample must contain less than 0.5 per cent of skins and coarse particles, and less than 5 per cent water.
Liquid driers must satisfy certain specifications. The drier, after being stored at 60º-70º F. for a week in the dark, in a closed container, must be clear and free from deposit. It must not contain more than 80 per cent turpentine and white spirit. The drier must not be darker than an agreed standard sample, when compared in similar glass tubes and viewed transversely in transmitted light. The flash point of the drier must be below 78º C. The drier must not show any precipitate when left to stand at 60º-70º F. for six hours with twenty volumes of raw linseed oil, and also with sixteen volumes of raw linseed oil and four volumes of white spirit.
THE USE OF DRIERS IN PRINTING INKS
Liquid driers are available from a number of reliable makers, e.g. 'Curgon' driers from Scott Bader. They are usually made and prepared by somewhat special methods, but the percentage metal content (i.e. 5 per cent) is known.
Cobalt paste driers used in printing-ink making usually contain a fair prcentage (10-20 per cent) cobalt linoleate or other cobalt liquid drier and 25 per cent of mixed metal acetate and borate ground into linseed stand oil varnish to produce a smooth and homogenous paste. The paste drier consequently consists of a minor soluble driers constituent and a major insoluble drier feeder. The soluble drier makes the drier active, while the feeder tends to decompose and feed lead, cobalt, or manganese metal in an active state to the drier. In other words, the feeder slowly decomposes in the acidity of the varnish. These paste driers can decompose faster than carbon black can absorb driers. Carbon black letterpress inks containing paste as well as liquid driers always have the same drying time after any period of storage, as the paste driers have generated enough drier to the ink to counterbalance the amount of drier absorbed. Most letterpress inks work best with a mixture of liquid and paste driers adjusted so that the inks have a satisfactory drying time as measured on the testing machines. Liquid driers are appreciably acidic, with acid values of about seventy, and this is too acid for litho offset inks. Appreciable liquid drier in an offset ink causes it to scum badly, consequently paste driers, and only a low concentration of liquid driers, are used. In many litho-offset inks, paste driers only are included. It has already been mentioned that printing inks are treated with driers until the drying time is satisfactory.
The concentration of 5 per cent liquid driers in an ink normally varies from 0.5-3 per cent, and the amount of paste driers used varies from about 1-4 per cent. An ink which contains both driers might contain 1.5 per cent liquid driers and 2 per cent paste driers. These figures are only intended to convey a general picture of the amount of driers introduced into an ink, and obviously a great deal depends on the general drying properties of the medium.
If paper has been treated with a small amount of cobalt sulphate during its manufacture, it is known to have better drying properties than untreated papers. It is possible that paper makers will develop treatments during the making stage and produce papers on which the ink will dry in a considerably shorter period of time; the inks used will still have the usual drying time on the machine.
Ink on Surfaces other than Paper
GENERAL PRINCIPLES
A VITAL property of an ink is good adhesion to the printing surface after drying. Many surfaces are more difficult to print than paper because the normal types of ink adhere very badly. Inks adhere better to rough surfaces where some mechanical interlocking is possible, consequently formulating inks for cloth, felt, and wood presents no serious problem. With very smooth surfaces such as Cellophane, polythene, P.V.C., and Bakelite, only physico-chemical forces are available for adhesion and, moreover, the surface enery of this type of material is usually completely compensated, leaving little free surface energy available for interfacial reactions of the type required to bind a film of ink to the surface. The ink must be responsible for imparting sufficient free energy to the smooth surface to form an adequate adhesive bond, not only under wet conditions, but when the ink is thoroughly dry and the print has aged. The general principles which can be used to promote the adhesion of an ink to a difficult printing surface are:
(1) Thermoactivate the surface
Heating the surface, before or after impression, often improves the printing quality. The adhesion of an aniline ink to Cellophane is always promoted by passing the printed web over a hot roller.
(2) Incorporate in the vehicle either a solvent or a swelling agent for the surface
Glycol-ether solvents are used in inks for cellulose acetate film, as they soften the printing surface. An evaporating solvent can normally only be expected to make the ink adhere when wet, due to some of the solvent being present, and not when the ink is dry; unless the surface is softened and slightly distorted by the wet ink, enabling it to key on the the mildly attacked surface and adhere fairly well under dry conditions. Blistering of the surface, or other defect, due to fierce attack, must be avoided. In other words, a solvent for the surface, present in the ink vehicle, may promote adhesion by causing optimum softening, roughen-ing, or altering the surface below the printed film of ink.
(3) Use a resinous binder in the vehicle compatible with the material to be printed
A suitable ink for P.V.C. printing must be based on a resin compatible with P.V.C., otherwise the ink film will adhere only in the presence of a solvent or swelling agent for P.V.C. A common technique is to use P.V.C. powder dispersed in a suitable solvent or swelling agent. Similarly, a vehicle for polythene film can be made by dissolving polythene in toluene or decahydronaphthalene and adding a stabilizer, such as lithographic varnish, alkyd resin, or polyisobutylene (German Patent 898,906).
(4) Use a resin of maximun polarity
Viscous film can be printed with nitrocellulose or shellac inks, because of the intrinsic polarity of these resins. Inks for smooth plastic materials sometimes contain resins of high acid value. If using a polar resin in an ink leads to inadequate press performance, this may be overcome by changing the process, e.g. print the work letterpress instead of offset.
(5) Use a polar solvent
A ketone, alcohol, or other organic solvent which contains polar functional groups, should be better than mineral oil or white spirit.
(6) Ensure optimum plasticity
The plasticity of the ink should be similar to that of the surface, to avoid any tendency of the dried ink to crack or flake. Adhesion is improved in some cases by introducing a small amount of plasticizer into the medium.
(7) Print by a two-stage process
If the surface is underprinted with a clear varnish formulated to be practically invisible or else roller-coated with a stoving enamel, overprinting may be an easy matter.
(8) Test the trial ink thoroughly
The trial ink should be carefully tested on the surface and the formulation improved from the practical experience gained from laboratory tests and machine trials.
Finally, it should be pointed out that the difficulty in formulating suitable ink for a smooth surface is often one of degree. An ink suitable for Cellophane is easier to formulate than an ink for Bakelite, which is an exceptionally difficult surface, as it is very smooth, insoluble, infusible, and can provide no free surface energy, leaving little scope for the ink maker except the use of heat and polar materials. In a more general case, such as an ink for smooth rubber sheeting, an ink containing rubber dispersed in a swelling agent for rubber should prove adequate, provi-ding the ink does not damage the printed material, is suitable for the process and does not cause trouble on the press.
CELLOPHANE PRINTING
Printing inks for cellulosic materials-celluloid, Cellophane, and highly glazed transparent papers such as glassine-present special problems due to the thickness of the sheets which prevent them from clinging well to the inked forme in some cases, and the non-absorbency of the printing surface which causes drying and adhesion problems. Drying oils are unsuitable because they are long drying, and give scratchable films of poor adhesion. The ink used should have a slight solvent action on the material so that it penetrates the surface and sets within the top surface. It is customary to use a plasticizable base, and a liquid which is a solvent for both the printing surface and the ink constituents. The medium may include a cellulose derivative or a natural or synthetic resin. Cellulose esters and ethers have been employed, including nitrocellulose, acetylcellulose, methylcellulose, and cellulose butyrate. A low viscosity ester penetrates the surface better. A combination of a cellulose ester with resins can be effective, such as cellulose nitrate or acetate with ester gum or copal. To produce a smoother, more coherent film, as well as to help some penetration by softening the printing surface, plasticizers are added in some cases. Suitable plasticizers are tricresyl phosphate and dibutyl phthalate. Often small amounts of volatile solvent, such as acetone, alcohol, or ethyl acetate, promote the solution of the surface in the plasticizer. Suitable solvents are butanol, diethylene glycol, diacetone alcohol, methyl ethyl ketone, and the cellosolves. By using a mixture of two or more solvents of different evaporation rates the drying rate of the ink can be varied and controlled. Gentle heat can be applied to the prints to assist adhesion.
Cellophane is a transparent film of regenerated cellulose specially made by forcing a viscose, cellulose xanthogenate, through a long thin slot in an acid bath. It is not waterproof unless it is specially treated. Some inks have been set on Cellophane by dipping the undried print into molten paraffin wax at l00º C. In such cases, the ink should contain dimethyl phthalate, or other high-boiling solvent, miscible with the hot wax. The solvent is absorbed by the hot wax and the pigment is precipitated.
White Cellophane L/P Ink
|
Percent |
Rutile |
60 |
Wood oil phenolic |
30 |
Refined linseed oil |
9 |
Mild driers |
1 |
|
100 |
A great deal of Cellophane is printed aniline, using shellac in alcohol media and including up to 3 per cent plasticizer. The prints should be passed over a hot roller at about 100º C. to aid drying and improve adhesion.
MOISTURE-PROOF VISCOUS FILM PRINTING
Moisture-proof viscous film or moisture-proof Cellophane is hydrophilic in nature and is usually coated with waxed or unwaxed nitrocellulose lacquer. It is normally printed gravure as well as aniline, and is easily wetted and often softened by the solvents in those inks. Suitable solvents are alcohols and esters of low surface tension and boiling point, which are preferably compatible with the nitro cellulose lacquer to help adhesion. The prints should be passed over a steam-heated roller as quick drying promotes adhesion. Rollers heated to l20º-l30ºC. should not be used as nitrocellulose discolours at these temperatures.
POLYETHYLENE OR POLYTHENE FILM PRINTING
Polythene provides a hydrophobic, inert hydrocarbon surface which melts about 105º C. A medium of low polarity thinned with hydrocarbon solvent should be used. Adhesion is aided by cautious heating to ensure blending the ink film with the underlying surface. Such prints are seldom good on rub-resistance.
Polythene-coated paper and plastic film are now available and manufacturers of packaging inks are keeping a keen eye on this development. The Telegraph Construction and Maintenance Co. Ltd. (Telcon) coat paper with a one-thou polythene film by an extrusion process, e.g., 30-40 lb. D.C. Kraft used for paper sacks, and manufacture Teleophone, which is regenerated cellulose film coated with polythene; the cellulose film is very impermeable to gas and the polythene film is very impermeable to moisture. Polythene-coated aluminium foil has become a populat wrapper.
PRINTING ON LACQUERS AND VARNISHED SURFACES
The inks should partially penetrate the surfaces by softening or dissolving the top layer of the coating. Shellac films should be printed with a medium of dibutyl phthalate and some ethyl lactate in alcohol. Nitrocellulose lacquer coated sateen requires a medium of nitrocellulose dissolved in methylated spirit, butanol, and some ethyl acetate. Another method advocated is to use cellulose ester or ether dissolved in water-soluble glycol mono-or di-formates (Brit. Pat. 311, 795; 1928).
PRINTING ON RUBBER
The pigments and driers used must be free of lead, iron, copper, or manganese, since they form dark sulphides and react on vulcanization. Chrome pigments tend to leave an after tack, but cadmium yellows and ultramarine are suitable pigments. Solvents which swell rubber must be avoided, notably petroleum ether and benzenoid hydrocarbons. In most cases the unvulcanized rubber is printed, dusted with powdered sulphur, and vulcanized after printing. Printed transfers have been used and removed after vulcanization. The Callender Cable and Construction Co. Ltd. mark rubber by a similar method, Bowyer (Brit. Pat. 347, 620; 1928). Rubber has been printed by penetrating inks, alcohol-soluble induline dissolved in tetrahydronaphthalene with some methyl-ethylene glycol being used (Allman and Norris, Brit. Pat. 296, 461; 1927).
PRINTING ON P.V.C.
If P.V.C. is polymerized in the absence of interpolymer components a white powder results which softens at 90º C. and has to be shaped at about 150ºC. To prevent decomposition and discolouration when the substance softens, a heat stabilizer is used, such as lead compounds, sodium carbonate, and diphenylthiourea. Dilute solutions can be obtained in chlorinated hydrocarbons, dioxan, and cyclohexanone. The substance can be plasticized with up to 50 per cent plasticizer, such as T.C.P. and D.B.P., and worked into a plastic mass at 130º- 150º C. to give sheets which are resistant to acids, alkalis, and oxidation.
Letterpress inks for P.V.C. printing can be based on vinyl resins; the solvents present in the ink soften the P.V.C. sheets and this ensures good adhesion. A great deal of P.V.C. is printed silk-screen; this has been dealt with in the chapter on screen inks.
PRINTING ON METAL AND METAL FOIL
Aluminium has a good affinity for oily inks and ordinary drying oil inks can be printed on the metal. Alkaline pigments should be avoided as aluminium is amphoteric in character, but the metal is passive to weak acids. The underlying sheen of the metal reinforces transparent inks with a fascinating brilliance. Transparent aniline inks printed on such foil are suitable for Easter-egg wrappings because of the attractive appearance. Inks must have good adhesion and full colour strength to ensure the best results, particularly with very glossy foils. The surface is non-absorbent and either letterpress inks drying by chemical methods, or suitably formulated gravure or aniline inks must be used. The film should be cleaned and free from grease; the vapour of trichlorethylene is an efficient degreaser. Printing on a varnish film of nitrocellulose or synthetic resin is easier, but deliberately to make the printing a two-stage process is unduly expensive and should be avoided. A lacquer drying by heat hardening can be used to print on either the printed or unprinted area to obtain a special type of effect. In gravure printing of foil, the printed metal is passed over a heated cylinder to aid drying and improve adhesion. Trichlorethylene is useful in gravure inks for foil and Cellophane printing, as it speeds up evaporation and leaves a more brilliant print. Methyl cellosolve is often added in small amount. Paralac 21 in methyl ethyl ketone can be used as a gravure foil medium.
PRINTERS' USE FOR ROLLER COATING
Offset lithography was first introduced into Great Britain in the middle of the nineteenth century specifically for tin printing. Frequently tin printers had to produce masses of white or tinted backgrounds and this could not be done economically or very easily. A white offset tin-printing ink has to have a suitable consistency and flow, must contain about 60 per cent rutile for adequate whiteness and opacity due to the small lift of ink, must not contain materials which damage the press rollers or blankets, must give hard films after stoving, while good gloss may also be expected. Good gloss is difficult to achieve due to the high pigmentation and limited amount of medium, while the latter must not be tacky as tackiness builds up on the machine and lowers the printing quality, due to erratic splitting of the ink film at impression. Even when a suitable white ink has been formulated it will not be cheap, and printing masses of solid forme offset, often the entire sheet of tin, is too expensive for normal commercial consideration. Further, intense white backgrounds are impossible at one impression as offset films are too thin. The modern method adopted is to print the solid background on a roller coating machine and not only white and tinted inks but any colour ink can be printed.
Roller coating has the following advantages:
- The machine used is simple in design, occupies little space and is easy to operate.
- Very even films can be printed if the machine is set properly and the ink is properly formulated. If the coating is badly formulated, it is possible to obtain a ribbed film of ink on the rollers which is transmitted to the panels during coating and if the ink has poor flow-out the coating dries with a crinkled appearance.
- Not only thick films, but films of a required thickness can be accurately obtained by careful setting of the machine, thus ensuring the opacity required. This enables a lower percentage pigmentation to be used in the coating, e.g. 30 per cent rutile, and also avoids any necessity for printing several times to obtain thick films.
- A wider range of solvents can be used, e.g. esters, ketones, aromatic white spirit, or mixtures of solvents.
- A wider range of resins can be used, due to the opportunity to choose from an extended range of thinners.
- High gloss is much easier, due to the lower pigmentation and wider choice of materials.
- It is cheaper than offset tin printing.
- Stoving vehicles can be used which give a harder finish, while possessing adequate flexibility and exceptional adhesion to the sheet of metal.
Roller coating machines can be used for the utterly different process of overprinting transparent nitrocellulose lacquers which, since they contain alcohol and cellosolve solvents, cannot be printed offset. Such lacquers are colourless and dry with a good gloss in about fifteen minutes by solvent evaporation. The inks used for the original printing must not bleed in nitrocellulose. By not staining the paper and by having an exceptionally quick drying time, these varnishes are superior to oleoresinous varnishes. If the coated film is rather thick this method will not be cheap and production is much slower than offset for a long run. Using better colour overprinting varnishes does not matter, except above pale tints and bare stock, and a drying time of four hours is rarely a handicap to lithographers providing the sheets do not stick in the stack. Roller coating never gives quite as smooth a film as offset printing, but the quality of the work is good and in selected circumstances it is cheaper and more expedient.
ROLLER COATINGS
Most roller coatings are whites, supplied at 5 p. viscosity, and should have excellent properties when stoved at 120º C. for twenty minutes. A roller coating clear should stove under these same conditions to produce:
- Perfectly clear films.
- Films of excellent scratch hardness.
- Films as near water-white as possible.
- Films of good colour retention.
- Films of good flow properties.
- Films of good adhesion to tin plate.
- Films which are satisfactory in bending and in tin lid stamping tests. This implies good flexibility. Stamped lids should be autoclaved to see whether any faults develop, such as cracking off or peeling.
- Good films when staved in a foul oven at 120º C. for twenty minutes. This oven is heated with a luminous flame through a small entrance hole, and has no vent or chimney. The films should be free of rivelling and gas checking defects.
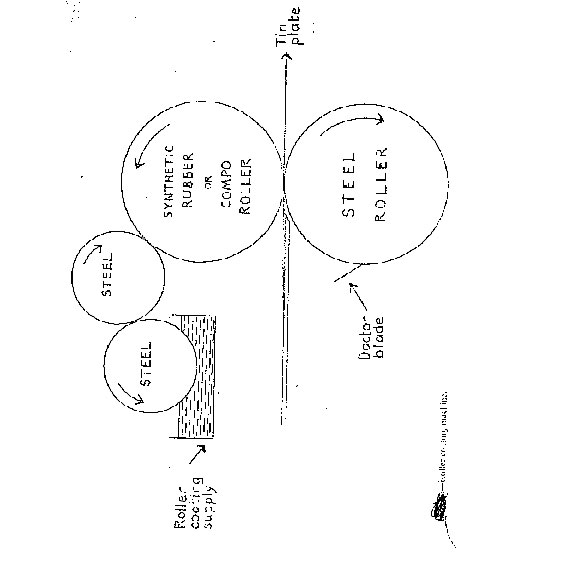
Pigmented roller coatings should be tested after stoving at 120º C. for twenty minutes.
- The hardness should be tested using a scratch hardness tester and the Sward Hardness Rocker,
- They should have good flow,
- Good adhesion to the underlying surface,
- Good flexibility as shown in the tin lid-stamping test,
- Good colour retention on stoving for an hour at 120º C. and when stoved at l80ºC. for a short period,
- Good storage conditions and freedom from skinning in the tins,
- Solvents of reasonable odour, and which evaporate completely on stoving.
The most widely used solvents seem to be white spirit and aromatic white spirit, although methyl isobutyl ketone and cellosolve solvents are sometimes used. Suitable resins are the vinyls, 'Epikote' esters, and alkyds. Many alkyds used are about 50 per cent oil alkyds. The whites are usually pigmented with titania at about 27-38 per cent pigmentation, and often carry 28-30 per cent varnish solids. Sometimes the varnish solids are much higher at about 40 per cent. Guaiacol has often been included as a anti-skinning agent to stop thick skins forming when the roller coating is stored in cans. The roller coatings are normally tested on sheets of clean tin plate which are coated by feeding through a roller coating machine.
Long oil length alkyds are flexible but do not stove to a hard finish in twenty minutes. Alkyds can be blended with a hard resin varnish to produce a product which is hard and stamps well.
I.C.I. Roller Coating Medium
|
Percent |
Bedesol 72 |
20 |
Paralac 67 |
28 |
46 p. D.C.O. |
22 |
White Spirit |
26 |
Cellosolve |
4 |
|
100 |
The Bedesol 72 and the dehydrated castor oil are heated together to 260º C. and held on temperature until a varnish bead on glass remains clear. The time necessary is about ten minutes. The Paralac 67 is added, the temperature is raised to 260º C. and kept there for five minutes. The heating is stopped, and the thinners are added at about 140º C.
I.C.I. White Roller Coating Medium
|
Percent |
Titanium Dioxide Kronos Grade E |
39.7 |
Roller Coating Medium |
45.3 |
White Spirit |
13.0 |
Cellosolve |
1.5 |
6 per cent Cobalt Naphthenate |
0.5 |
|
100.0 |
Paralac 64 is recommended by I.C.I. as an excellent medium for roller coating enamels, since it gives hard glossy films with excellent adhesion and stamping properties. It is a short-medium oil length, drying castor oil modified alkydi with an A.V. of 25, and phthalic anhydride content of 39 per cent. Paralac 64AH is a 50 per cent solution of Paralac 64 in a high-boiling aromatic hydrocarbon solvent; it has a viscosity of 75 p. at 20º C. The solvent used is practically colourless, and has less smell and a higher flash point then xylene; the use of a higher boiling solvent results in improved flow yet has no appreciable effect on stoving schedules at 120º C.
I.C.I. White Roller Coating Enamel
|
Percent |
Rutile ('Rutiox' HD) |
29.5 |
Paralac 64AH |
47.2 |
White spirit |
21.0 |
Diacetone alcohol |
2.3 |
|
100.0 |
Pigment: Total Solid Resin=1.25:1
Viscosity: 150 seconds, No. 4 Ford Cup, at 20º C.
Flash Point: 109º F. (43º C.).
No drier need be used for a stoving schedule of twenty minutes at 120º C.; this ensures improved colour and colour retention. Adhesion can be improved by adding Bedesol 74 to give a Paralac 64: Bedesol 74 ratio of 4:1 calculated as solid resins, preferably as a 50 per cent solution in part of the white spirit.
Vinyl copolymer resins made by copolymerization of vinyl chloride-acetate copolymers (e.g. Vinylite, Geon Resins 400 series), vinyl chloride and vinylidene chloride (e.g. Geon Resins 200 series), or vinylidene chloride and acrylonitrile (e.g. Saran Resin F120), can be used for roller coatings but strong solvents of suitable boiling range, such as Sextone (cyclohexanone) or Sextone B (isomeric methylcyclo-hexanones), must be employed; such varnishes can be thinned with toluene and xylene. A reduced rate of evaporation can be secured with Sextone Z, a mixture of the isomeric dimethylcyclohexanones, which is an effective solvent of adequate solvent power.
The introduction of say 10 per cent of Howards Resin MS2, which is a neutral pure cyclic ketone synthetic resin ('cyclohexanone resin'), melting at 85º C., into vinyl polymer formulations appreciably reduces the viscosity of the vehicle for a given solid content, and enables more binder to be introduced into the coating; the gloss is improved, and better adhesion is obtained to glass and metal surfaces. Howards cyclic ester plasticizers (e.g. Plasticizer B.S.), are suitable in these formulations since they are of solvating type, low volatility, and low migration.
Howards Roller Coating
Stoving schedule: 12 minutes at 180º C., or 20 minutes at 120º C.
|
Percent |
Pigments |
1-10 |
Vinylite VMCH |
13 |
Howards Resin MS2 |
2 |
Howards Plasticizer B.S. |
3-4 |
Sextone B |
15-25 |
Propylene oxide |
0.2 |
Heat stabilizer (for P.V.C.) |
1 |
Methyl isobutyl ketone |
20 |
Toluene and/or Xylene |
30-40 |
The vehicle is made by dispersing the vinyl resins thoroughly in aromatic hydrocarbons before the Sextone B and other active solvents are added.
Heat-set emulsion inks have been patented by Clark (Brit. Pat. 654, 535; 1948). The following is magazine ink:
Parts
Zincated Resins |
45 |
Paraffin Wax |
2 |
Dissolve in Petroleum (470º-500º F.) |
25 |
Amine |
1 |
Then add: Water |
25 |
Carbon Black |
15 |
Lamp Black |
8 |
Milori Blue |
5 |
Another type of ink is mentioned:
COLD-SET INKS
Another type of letterpress ink designed for fast drying, are the cold-set inks: these inks dry by solidification. The prints are produced at a temperature above the melting point of the vehicle.
The ink is based on a pigment dispersed in a plasticized wax and printed molten at about 110º C., and setting at about 80º C. These inks were originally used to print textiles with iron on transfers'; they have been formulated for gravure as well as typographic presses.
They have the advantages of overcoming show-through, strike-through, and first impression offset; and do not skin in the cans, are tack free when liquid, and do not dry on the press. They yield good prints, since some of the ink does not drain and spread into the fibres of the paper.
Their disadvantages are most serious. The fundamental method using an ink above 100º C. results in an inconvenient and costly press. Further, press parts do not uniformly expand with rise of temperature, and machine wear is excessive. For these reasons the inks have never come into general use, and are reminders of an obsolete trial.