EPOXY RESINS
INTRODUCTION
In the plastics industry epoxy resins are classified as thermosetting resins, and they are used in the paint industry as convertible coatings. Epoxy resins are cured and converted to a thermoset state by chemical reaction between the resin and a curing agent. Depending on the curing agent this reaction can take place; either at elevated or at room temperatures. The cured resins are not soluble in solvents and cannot be melted by heating. This property is in direct contrast to thermoplastic products, such PVC, or polystyrene or non-convertible coatings, such as chlorinated rubber, acrylic or nitrocellulose lacquers which remain soluble in solvents and can be remelted by heating.
Epoxy resins became commerecially available in Australia in the early 1950s and since that time have become firmly established in many industries. Most commonly used types are based on epichlorhydrin and diphenylol propane and are available in range of molecular weights. The low molecular weight resins are liquid and the high molecular weight resins are solid.
What are the main properties of the epoxy-resin-based systems that influence the choice of epoxy resins from a wide range of plastics available at present? The important properties are listed below.
- The chemical structure of epoxy resins gives them high chemical resistance against a wide range of severe corrosive conditions. These properties are derived from the aromatic nature of the backbone and good chemical stability of the phenolic ether linkage.
- Epoxy resins have good adhesion to a wide range of materials, including metals, wood, concrete, glass, ceramic and many plastics. This is due to the presence of polar groups in the cured resin.
- Low shrinkage during curing results in good dimensional accuracy in construction of structural items and enables manufacture of high strength adhesives with a glue line of low residual stress.
- Ease of fabrication means that complicated shapes can be reproduced easily using liquid epoxy resins systems which can be cured at room temperatures.
- Good physical properties such as toughness, flexibility and abrasion resistance can be obtained.
- Although there are temperature limitations, epoxy resins are generally superior to almost all thermoplastics in elevated temperature performance.
One of the main users of epoxy resins is the paint industry, which produces special types of surface coatings which will be discussed in further detail below. The electrical industry was one of the first industries where epoxy resins became established during the early stages of commercial production. Epoxy resins are convenient to use in solvent-free liquid form which sets into a hard infusible solid after the addition of curing agent. They are used extensively, for example for potting, embedding or encapsulation of electrical components, for cable joining to make water proof joints, for manufacture of Telecom terminal pillars.
Another industry to recognize the value of liquid epoxy resins was the engineering industry. Low shrinkage and good dimensional stability in service are important properties utilized for manufacture of foundry patterns, vacuum forming moulds, press tools for prototype or short runs, drilling jigs, and checking fixtures. Adhesives are used in many applications in place of soldering, bolts or rivets, particularly in small parts assembly and in aircraft construction. Fibreglass reinforced plastics are manufactured from epoxy resins for applications where chemical resistance and good physical strength properties are the main requirements, for example piping and storage vessels in the chemical industry. In the civil engineering industry the use of epoxy resins has also become established as a standard practice. The rapid cure of epoxy adhesives as compared with cement and good adhesion to new and old concrete enables more rapid construction and repair of concrete structures.
EPOXY RESIN MANUFACTURE AND CHARACTERIZATION
By far the most important class of epoxy resins used at present on a large scale commercially is that based upon the reaction between diphenylol propane and epichlorhydrin in the presence of alkali. The basic reactions are shown below.

The basic reaction is formation under alkaline conditions of a chlorhydrin ether of DPP (b) followed by dehydrochlorination of the chlorhydrin group by alkali to form an epoxy group, thus giving the diglycidyl ether of DPP (c). An excess of ECH will favour a high proportion of the simple diglycidyl ether of DPP; higher DPP ratios will give higher molecular weight polymers. Commercial grades of resin can be represented by the following formula:

The pure diglycidyl ether of DPP with n=0 is a crystalline solid. The commercial low viscoity liquid resins are rich in this compound and the average n is approximately 0.2. Viscosity can be further reduced by addition of monoepoxide compounds such as aliphatic glycidyl ethers. In low melting point solid resins average n is approximately 2. The common commercial high molecular weight resins have average n up to 13. There are also very high molecular weight resins with molecular weights up to 200 000. These resins have mainly hydroxy groups and practically no epoxy groups and are used as thermoplastic resins for non-convertible coatings.
The commercial epoxy resins are characterized by specifying their main properties, as in sections 2.1 to 2.3.
Epoxide Group Content (EGC)
This is at present expressed as millimoles of epoxide groups per 1 kg of resin (m mol/kg). Previously this was expressed as Epoxy Molar Mass (EMM) in which case the unit is grams per mole of epoxide (g/mol). Conversion to EGC from EMM can be done by the following formula:
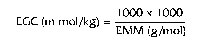
Hydroxyl Content
This is expressed as millimoles of hydroxyl groups per 1 kg of resin (m mol/kg). For esterification purposes, one epoxy group is equal to two hydroxyl groups and this must be taken into account when calculating esterification equivalents.
Viscosity
Commonly used metric viscosity unit is the Pascal second (Pa s), which has replaced the Poise unit (1 Poise = 0.1 Pa s).
Viscosity is normally measured at 250C on liquid low viscosity resins without dilution. A 70 per cent solution is used for high viscosity liquid resins and a 40 per cent solution is commonly used for solid resins in solvents such as glycol ethers. Properties of a typical range of epoxy resins are shown in table 1.
Selection of the resin grade depends on the application. Low molecular weight resins are rich in epoxy groups and are used for applications where the cross-linking reaction is through epoxy groups. In high molecular weight resins, hydroxy groups are predominant, and reactions involving both hydroxy and epoxy groups are selected for further polymerization and cross-linking.
CURING AGENTS FOR EPOXY RESINS
The reaction for cross-linking epoxies resins can be between epoxy resin molecules with the aid of a catalyst. However, a majority of uses of epoxy resins employ a reactive hardener (such as amines, acid anhydrides, phenolic resins) which combines with epoxy or hydroxy groups in the resin, to form a thermoset product.
Table 1 : Properties of a typical range of epoxy resins
Typical viscosity range pa. s
| Resin Grade | App. n | App. EMM g/mol | App. EGC m mol /kg. | Solids % Mass |
1. |
Low viscosity liquid resins modified with monoepoxide diluents |
0.2 |
200 |
5000 |
0.6-1.8 |
100 |
2. |
Low viscosity basic resins |
0.2 |
200 |
5000 |
0.8-16.0 |
100 |
3. |
High viscosity resins |
0.5 |
250 |
4000 |
0.4-1.0 |
70 |
4. |
Solid resins: |
|
|
|
|
|
|
Durrans Melting point approx. 700C |
2 |
500 |
2000 |
0.1-0.2 |
40 |
|
Durrans Melting point approx. 1000C |
4 |
900 |
1100 |
0.5-1.0 |
40 |
|
Durrans Melting point approx. 1300C |
9 |
1700 |
600 |
2.0-3.5 |
40 |
|
Durrans Melting point approx.1500C |
13 |
2700 |
370 |
4.0-12.0 |
40 |
The most commonly used curing agents for room temperature cured systems are polyfunctional amines and polymide resins. As shown below the active hydrogen atoms of primary and secondary amine groups react with epoxy groups.
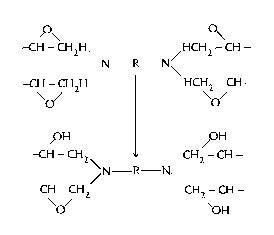
A primary monoamine has a functionality of 2 for epoxy reactions, whilst the epoxy group has a functionality of 1. Thus a diepoxide reacted with a monoamine would give a linear polymer. Consequently, the useful curing agents are polyamines, such as:
|
Functionality |
Molar Mass |
Ethylene diamine (EDA) |
4 |
60 |
Diethylene triamine (DET) |
5 |
103 |
Trietylene tetramine (TETA) |
6 |
146 |
The reaction mechanism suggests that the curing agent should be used in stoichiometric proportions. For example resin having an EMM of 190 the amount of DET would be:
This is normally expressed as parts by mass of curing agent for 100 grams of resin (phr), that is 11 phr of DET. The use of incorrect proportions can lead to water sensitivity and poor physical properties if an excessive amount of amine is used. Quite small excess amine will adversely affect the water sensitivity. Low curing agent content would result in poor solvent-resistant and poor physical properties. With solvent-free systems this can be conveniently checked by determining Deflection Temperature (DT), that is, the temperature at which a standard sample begins to distort under load when determined by a standard method. The optimum curing agent ratio will show a peak in the DT curve plotted from a range of determinations using different curing agent proportions.
In practice, the use of free low molecular weight aliphatic amines is undesirable because of problems caused by objectionable volatility of such amines from an industrial hygiene point of view. This volatility can be eliminated by prereacting the amine with part of the epoxy resin forming a so-called amine adduct. Amine adducts are usually prepared by mixing one molecule of epoxy resin with two molecules of polymine.
Using solid epoxy resins, so-called 'isolated adducts' are prepared by reacting in solution and then distilling the excess amine and solvent. Isolated adduct is a solid, usually marketed in powder form. If solvent and the excess amine are not removed, the amine adduct is described as an 'in situ adduct'. The main advantages of adducts compared with straight amines are :
- reduced volatility,
- reduced toxicity,
- reduced blushing tendency during cure of films, and
- smaller mixing ratio with resins reduces chances of error.
Cycloaliphatic amines form another group of curing agents that are less volatile than linear aliphatic amines. They are slower in curing and require additions of accelerators, or must be cured at elevated temperture.
Another method for eliminating the problems associated with the use of free amines is the use of polyamide resins. These are produced from dimeric fatty acids and amine, and are available in several grades of different molecular weights. Polyamide resins react with epoxy resins through amine groups present in the resin. Because they have higher molecular weight than straight amines, their mixing proportions are much higher. The mixing ratio can be varied within comparatively wide limits depending on the properties desired in the end product. Higher proportions of polyamide resin give increased flexibility; a lower ratio imparts best water resistance, but caution should be exercised in adjusting the proportions to ensure that achievement in one desired property does not make too much sacrifice in another requirement. The main advantages and disadvantages of polyamide resins compared with amine or amine adduct systems are :
- volatility: non-volatile,
- mixing ratio with eposy resin: lower with polyamide resin,
- pot life: longer with polyamide resin,
- flexibility: lower with polyamide resin,
- hardness: lower with polyamide resin,
- water resistance: higher with polyamide resin, and
- chemical resistance: lower with polyamide resin.
Ketimines are used as curing agents for applications where longer pot life is required. Ketimines are described as latent curing agents, as they do not react with epoxy resins until free amine is released by contact with moisture in the air during and after application. The film thickness of these systems should not exceed 250 um to allow moisture penetration during curing.
One disadvantage with the curing agents described above is that the rate of reaction becomes too slow at lower temperatures. Below 150C ambient temperature, adequate cure is not obtained with most of the conventional curing agnets. However, several special curing agents are now available which cure at much lower temperatures. Some of these are based on aromatic amines such as 4, 4-diaminodiphenyl methane (DDM) containing modifiers and accelerators. These curing agents when mixed with liquid epoxy resins can be cured at 50 C and even below :
PRINCIPLES IN FORMULATING WITH EPOXY RESINS
Two-pack Systems
Two-pack epoxy systems consist of a number of components which are selected to achieve desirable properties in the end product. A brief description of the components that may be used is given below.
Epoxy resins. Low molecular weight solid resins are used in solvent-based paints. Liquid resins are used in solventless systems.
Curing agents
- Amine and amine adduct-for best chemical resistance.
- Polyamide- for best flexibility and water resistance.
- Ketimines-for longer pot life in high solids systems.
- Modified aromatic amines-for low temperature cure.
Accelerators. Accelerators are often used in polymide cured solventless systems. Phenols, tertiary amines and triphenyl phosphate are typical accelerators.
Flexibilizers. Flexibilizers are often used with epoxy resins to increase flexibility and impact resistance. Typical products are polyamide and polysulfide resins. As mentioned previously, polyamides act also as curing agents. Other flexibilizers include ester plasticizers, epoxidised oils, and coal tar.
Reactive diluents. Monoepoxide diluents, such as n-butyl glycidyl ether, can be used in small proportions to reduce the viscosity of liquid epoxy resins in order to improve handling properties. As these diluents are of low molecular weight and are mono-fuctional, they reduce the physical strength and chemical resistance of the cured systems.
Pigments and fillers. Epoxy surface coatings use conventional pigments and extenders provided they meet chemical resistance requirements. Epoxy-resin-based adhesives and flooring compounds often use coarser fillers such as sand.
Thixotropic additives. Conventional types of thixotropic additives are used in epoxy systems and include synthetic silica (Aerosil*, Santocel'*), hydrogenated castor oil derivatives (Thixcin*) and Bentones.*
Solvents. Solubility of resins varies with their molecular weight. Liquid resins are soluble in hydrocarbons whilst solid resins are soluble in mixtures of aromatic hydrocarbons with alcohols, ketones and glycol ethers.
Two-pack epoxy systmes can be broadly classified into five groups, 1 to 5.
Solvent-based coatings
These systems are based on a solid epoxy resin solution, either clear or pigmented to give a desired colour. The resin is cured by addition of an amine adduct or polyamide.
Two-pack solvent-based paints have a long pot life (at least 6 hours) and can be applied by conventional methods, such as brushing or spraying. The normal paint film thickness per coat is about 50 pm. They have excellent adhesion to steel, concrete, asbestors cement and most other surfaces. They are tough and resistant to a wide range of chemicals and solvents. The chemical resistance of amine-adduct-cured systems is superior to the polyamide-cured formulations. Polyamide curing agents give a longer pot life, great flexibility, and superior water resistance. The choice between these two curing agents depends on the end use requirements.
Solventless and High Solids Coatings
High labour costs in applying the solvent-based paints to obtain high film thickness led to the development of solvent-free systems. Fox instance, it would be necessary to apply five to eight coats of conventional solvent based paint to obtain a minimum 250 to 375 pm film thickness required for good durability under immersion conditions. The use of solvent-free systems reduces labour cost, eliminates solvent hazards and simplifies ventilation problems in confined spaces.
Liquid epoxy resins are used in the manufacture of these coatings together with special types of low viscosity curing agents. The early problems of extremely short pot life of solvent-free systems have been overcome by development of latent curing agents or new specialized equipment for paint application.
Latent curing agents are based on ketimines. With this type of coating it is possible to apply by brush or spray up to 250pm film thickness in a single coat on vertical surfaces without sagging. Although these coatings are often described as solventless, they contain small amounts of solvents, and should be more accurately described as high solids coatings. They usually contain over 90 per cent of film forming material.
Another method of overcoming application difficulties with solvent-free systems and to obtain better results is by using specialized equipment. Two-pack heated airless spray rigs (capable of accurately metering the components and of controlling their temperature at suitable levels) are now available. The temperature drop immediately after application of preheated paint gives a setting-up effect similar to that obtained by solvent loss with conventional paints. Solventless paints applied by other methods usually remain liquid for 2 to 4 hours until gelation takes place.
The chemical resistancce and corrosion resistance of solventless coatings is very similar to that of the two pack solvent based paints. They are, however, less flexible and show a more pronounced tendency to yellow and lose gloss on exterior exposure. Some of the solvent-free types are only available in darker shades because of the colour of the modified aromatic amine used to obtain good cure at low temperatures.
Tar Epoxy Coatings
Two-pack epoxy paints can be modified with suitable grades of tar to produce tar epoxy coatings. The addition of a comparatively low cost tar to an epoxy resin system improves water resistance, but some loss in chemical and solvent resistance occurs. The colour of tar epoxy paints is generally black; tars of very light colour have also become available to enable formulation of paints in a fairly wide range of colours for special applications where black is not acceptable.
The tar epoxy paints are formulated in the same manner as the unmodified two-pack epoxy paints and are available as conventional solvent-based systems or in high solids or solventless types. They can be applied by brushing, roller coating, or spraying, and they are particularly suitable for airless spray. The film thickness per coat can range from 50 to 375 pm, depending on the type of formulation.
Flooring Compounds
Concrete floors are often a cause of concern in industrial plants as conventional coatings are not always resistant to heavy wear or damage through the spillage of corrosive materials. For this applications, solventless liquid epoxy resin blends with a suitable aggregate can be used at a film thickness ranging from 3 to 6 mm applied in one operation. These compounds may be used in the construction of new floors or in resurfacing of old ones, and they may be laid on concrete, metal or wood substrates.
Several types of flooring compounds are available. One type consists of a compound heavily filled with sand or other aggregate, and it is applied by trowelling. Another method of application uses low viscosity compositions, which are poured directly onto the substrate and smoothed out to form a continuous level coating. Additional aggregate is then spread on the surface before the coating has set and is trowelled into the film to give a non-skid surface. A decorative appearance can be obtained by the use of conventional pigments. This type of flooring is used in chemical plants, dairies, breweries and other industries where a combination of chemical resistance, hard wearing surface, and skid resistant properties is required.
Fibreglass Laminates
Fibreglass-reinforced epoxies have outstanding physical properties and are well established in electrical applications and in aircraft and rocket construction. In corrosion protection, epoxy laminates for cladding and structural uses are normally based on room temperature cured systems manufactured by hand lay-up techniques. In the production of chemically resistant piping and tank construction, filament winding techniques have been established and are extensively used overseas.
Cladding with fibreglass-reinforced epoxies gives a chemically resistant coating that can be built up to higher film thickness than conventional coatings with superior physical strength properties, particularly in resistance to impact. It is a most satisfactory method for the lining and repair of concrete and steel tanks, and for wrapping pipes for protection and repair of leaks, without necessitating a shutdown.
Examples of Formulations (parts by mass)
SOLVENT BASED PAINT (9.4.1.1.)
Resin base : |
|
Epikote* 1001 X 75 |
43.0 |
Flow control agent |
2.3 |
Rutile titanium dioxide |
33.4 |
Solvent blend |
21.3 |
|
100.0 |
0
Hardener amine adduct: |
|
E.D.A. |
1.5 |
n-butanol |
6.0 |
Xylene |
6.0 |
Epikote* 1001 X 75a |
11.5 |
|
25. |
Slovent blend: |
|
MEK |
25 |
MIBK |
25 |
Oxitol* |
15 |
Toluene |
35 |
|
100 |
HIGH SOLIDS COATING (12.4.1.2)
Resin base : |
|
Epikote*215a |
100.0 |
Rutile titanium dioxide |
23.0 |
Barytes |
24.0 |
Diatomaceous earth |
9.0 |
Thickening agent |
1.8 |
Cresylic acid solution |
6.0 |
50 per cent in alcohol |
|
Hardener: |
|
Ketimine Curing Agent |
45 |
SOLVENTLESS TAX EPOXY COATING (12.4.1.3.)
Tar base: |
|
Liquid tar |
33.0 |
Polymid 75b |
14.3 |
Accelerator DMP30 |
1.4 |
Thickening agent |
2.4 |
Talc TX |
22.4 |
Resin base: |
|
Epikote 816a |
26.5 |
SOLVENTLESS COATING FOR APPLICATION BY HEATED TWO COMPONENTAIR LESS SPRAY EQUIPMENT
Resin base: |
|
Epikote*828a |
65.35 |
Synthetic iron oxide |
16.03 |
Asbestine 20 pm |
10.79 |
Microtalc |
5.35 |
Thickening agent |
1.49 |
Silicone resin R281 |
0.99 |
|
100.00 |
Hardener (aromatic amine): |
|
Epikure 153 |
41 |
Equivalent Products |
|
|
|
Epikote |
828 |
Aealdite GY 250 |
DER 331 |
|
815 |
MY 752 |
DER 334 |
|
Dx 215 |
LC 191 |
DER 324 |
|
1001 |
6071 |
DER 661 |
|
(Shell) |
(Ciba-Geigy) |
(Dow) |
Single-pack Epoxy Maintenance Paints
Epoxy Esters
The chemical structre of an epoxy resin molecule clearly shows its polyol nature. The secondary hydroxyl groups are spaced along the chain and each epoxy group is equivalent to two hydroxyl groups for the purposes of esterification.
The epoxy esters are generally manufactured from medium molecular weight epoxy resins with an EGC of approximately 1100, although lower and higher molecular weight resins are used. The properties of epoxy esters can be varied according to the degree of esterification with vegetable oil fatty acids, and the type of fatty acid used. Typical fatty acids are linseed, D.C.O., soya and tall oil. Short oil ester (30 to 50 per cent oil) are used for baking finishes and the medium and long oil esters are used for manufacture of air dry maintenance paints.
Epoxy ester maintenance coatings are used where comparatively mild corrosive conditions are encountered. They are similar to alkyd paints in drying properties, but show greater resistance to saponification and improved adhesion. They are widely used for interior and exterior protection of structural steel and exterior coatings for storage tanks in refineries and chemical plants.
Single-pack Thermoplastic Epoxy Systems
For some specialized applications, single-pack epoxy coatings are available, that differ from other types in that they are thermoplastic, non-convertible coatings. They harden purely by solvent evaporation and consist of epoxy resin of very high molecular weight dissolved in a suitable solvent.
Thermoplastic epoxies are of very high viscosity and are not as suitable for manufacture of finishing coats as the thermosetting epoxies. They are used mainly for the manufacture of highly pigmented primers, and they are particularly suitable as binders for zinc rich primers, as they give good resistance to settling on storage. The thermoplastic epoxies retain the high chemical resistance and the adhesion typical of epoxies, and have the advantage of being a one-pack formulation (similar to conventional paints). Their solvent resistance is limited, but the overcoating of primers on this resin is possible with practically all types of paints without danger of bleeding or lifting. Some softening of the paint film at elevated temperatures can be expected with thermoplastic epoxies and this should be kept in mind when considering practical applications.
Epoxy Industrial Baking Finishes
Solid epoxy resins of high molecular weight are used for manufacture of baking systems which are well known in the industrial finishing field. They are used for drum and tank linings, can coatings, domestic appliance finishes, and automotive primers.
Epoxy short oil esters are used in a similar way to alkyd resins in baking finishes, in applications when higher chemical resistance is required. High molecular weight resins with EGC lower than 600 are used for cross-linking through hydroxyl and epoxy groups using urea formaldehyde or phenol formaldehyde resins. These systems show extremely high toughness and are widely used for drum and can linings. They are baked at 2000C for 10 to 20 minutes to achieve full cure.
A new development in industrial coatings is epoxy powder coatings. The powders are manufactured by dispersing pigments and flow control additives and curing agent in a molten epoxy resin. On cooling, the blend solidifies to a hard, brittle mass, which is crushed and ground into a powder of the required particle size. Typical curing agents used for this application are based on dicyandiamide; they are solid and not reactive at room temperature. Another type of powder coating is based on a combination of epoxy and polyster resins. Powder coatings require baking at 1700 to 200 0C to form a thermoset finish.
The powders can be applied to articles by dipping the preheated object into a bath of the powder which is fluidized (by blowing air through a specially designed porous bottom of the bath) or by spraying the powder by flock gun. The most convenient method for application of powders is electrostatic spraying onto cold or preheated objects. The epoxy powder coatings have two main advantages compared with solvent-based systems:
- Absence of solvents reduces health and safety hazards.
- For special heavy duty applications, a high film thickness can be obtained in one application without danger of solvent retention or film porosity.
They are used for applications where severe corrosion conditions are encountered or where good electrical properties are important. They are becoming established in decorative coatings for application on articles of complicated shapes, such as tubular steel furniture and expanded metal articles, because of their toughness. Another use is for protection of pipelines for natural gas.
Many recent developments in industrial coatings are water-based systems. Most of the automotive primers are now applied by electrodeposition from a water dispersion of organic binder, which is negatively charged for anodic electrodeposition (or positively charged for cathodic electrodeposition). Suitably modified epoxy esters are used for both anodic and cathodic electrodeposition automotive primers.