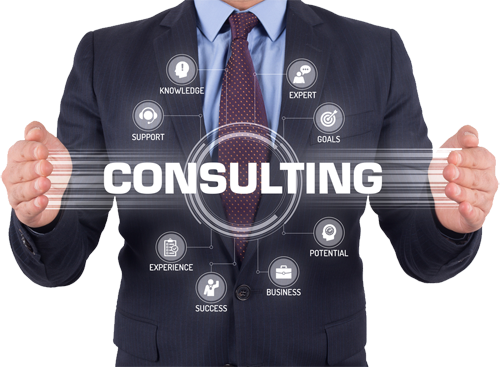
Woven PP (Polypropylene) Bags
Woven PP (Polypropylene) bags or woven PP (Polypropylene) bags PP bags, which are woven plastic bags mainly made of polypropylene, are commonly used for material packaging in industries such as fertilizer, cement, sand, rice, grains, sugar, cattle feed, and many others. Lighter weight, higher strength, and greater corrosion resistance are all advantages of PP woven bags/sacks.
Rice, spices, flour, fertilizers, sugar, agro products, and other materials can all be packed in these moisture-proof PP woven bags. These Sacks are commonly used in a variety of industries to package a diverse range of goods and raw materials obtained from suppliers and transported from one location to another.
These laminated polypropylene bags have a special extended shelf life that makes them more resistant to humid conditions, allowing the packed items to last longer. During filling, conveying, packing, and transportation, these bags withstand rough handling with almost no broken bags. Bags that are in good condition allow for fast handling, compact storage, and reliable transportation. The bags have a valve that allows for fast filling and self-closing operation.
Features of Polypropylene Bags suitable for Packaging of Cement
PP bags are produced by weaving thin strips of polypropylene in a weft and warp manner. However, PP bags may also be non-woven. Such bags are produced by fusing thin strips of polypropylene. Let us discuss the reasons for the high demand for these packaging bags in the cement industry.
1. Easy Availability
Earlier packaging bags were made from jute. Jute production has a seasonal variation. As a result, there were times when jute was in short supply for manufacturing packaging bags. However, polypropylene polymer is readily available throughout the year. This also has a lasting impact on supply chain. The market has never witnessed the shortfall of these bags.
2. Strong, Durable, and Long-lasting
Polypropylene has high tensile strength, and thus, can hold large quantities of cement without tearing. It is a sturdy material and lasts long. Thus, it is possible to reuse PP-based cement bags for a long time.
3. Impermeability to water
Jute bags become soggy and remain wet for long upon exposure to moisture. Cement is a substance that hardens upon exposure to moisture. It is impossible to mend cement once it is set. If, during storage or transport, cement encounters moisture, it will become useless. Thus, the packaging material for storing cement should be moisture resistant. Polypropylene bags create an impermeability barrier for water.
4. Tear resistance
While transporting cement, the labor requires handling the packaging bags swiftly. Innate resistance of polypropylene to tearing makes the handling of the packaged cement relatively easy. In the warehouses, the tear resistance of polypropylene packaging bags prevents rodents from damaging them. In this manner, polypropylene safeguards the internal contents from spillage and spoilage.
5. Chemical resistance
The quality of cement deteriorates by reacting with chemicals like alkali or acid. The packaging bags for cement should not degrade when exposed to chemicals and should not allow entry of chemicals inside the bag. Polypropylene is chemically inert, and thus, ideal for the packaging of cement.
6. Weatherproof
Packaged cement may be transported to different regions or during different seasons. The external layer of the packaging bag should be unaffected by the change in the weather. Polypropylene is a weatherproof plastic. Hence, it is suitable for packaging cement.
7. Lightweight
PP cement bag manufacturers choose polypropylene as the packaging material because it is light in weight. This property of PP makes it easy to handle.
8. Easy to stack
Polypropylene has anti-static and anti-skid properties. Consequently, packaging bags made from PP can be stored easily in warehouses. Gusseted PP bags are even easier to stack.
9. Affordability
Cement bags manufactured from PP are cheap. There are many plastics available for packaging use. Nonetheless, PP is the cheapest among them.
10. Customizable
Manufacturers can easily customize polypropylene bags. Easy to dye, PP bags can be manufactured in varying sizes. Printing, lamination, and addition of metalize layer is possible in polypropylene cement bags. Attractive packaging helps a brand in marketing their product better.
11. Eco-friendly
As polypropylene can last for a long time, it is possible to reuse the packaging bags made from it. After repetitive use, a PP-based packaging bag can be easily recycled into other useful plastic items. To increase environmental sustainability, the manufacturers may use natural dyes to produce colored PP bags.
Manufacturing Process of PP bags
Polypropylene Woven Bags & Sacks have become common due to their inertness to moisture, chemicals, and exceptional resistance to rotting and fungus attack as they are nontoxic and lighter in weight than traditional bags. Only pure virgin polypropylene resins are used in the manufacturing of woven polypropylene woven bags, and each bag is quality tested before being packed and shipped.
At any stage of the manufacturing process, complete quality control systems are strictly pursued. Extrusion of tape, fabric weaving, extrusion lamination, gravure printing, bag shaping, bag stitching, quality checking, and customer shipping are all part of this process. To ensure that our customers receive the highest foreign quality products, we aim to keep up with the current specifications for woven polypropylene sacks and FIBC bulk bags.
The key processes in the production of pp woven bags are extrusion, circular weaving, flexo printing, gravure printing, lamination, bag cutting, LDPE/HDPE inserting, gusseting, and bag sewing. To give you, our valued customers, a better understanding of how to make a PP woven wallet. Weaved polypropylene bags are the most used items in industrial packaging because of their strength, versatility, durability, and low cost.
They are widely used in packing grain, cereals-pulses, feeds, fertilizer, seeds, powders, sugar, salt, powder, and chemical in granulated form. PP Woven bags are made to the customer’s specifications in terms of mesh (9.9 to 16 x 16), denier (550 to 1800), GSM (as required), colour (as requested), and bag sizes ranging from 30 to 165 cm widths or depending on the desired capacity, as well as flat fabric sizes ranging from 60 to 300 cm widths or depending on the desired capacity.

Major Queries and Questions Answered in Our Project Report.
- What is HDPE/PP Woven Sacks industry?
- How has the HDPE/PP Woven Sacks industry performed so far and how will it perform in the coming years?
- What is the Project Feasibility of a HDPE/PP Woven Sacks Business
- What are the requirements of Working Capital for setting up a HDPE/PP Woven Sacks project?
- What is the structure of the HDPE/PP Woven Sacks Business and who are the key/major players?
- What is the total project cost for setting up a HDPE/PP Woven Sacks Industry
- What are the operating costs for setting up a HDPE/PP Woven Sacks project
- What are the machinery and equipment requirements for setting up a HDPE/PP Woven Sacks Business?
- Who are the Suppliers and Manufacturers of Plant & Machinery for setting up a HDPE/PP Woven Sacks Business?
- What are the requirements of raw material for setting up a HDPE/PP Woven Sacks project?
- Who are the Suppliers and Manufacturers of Raw materials for setting up a HDPE/PP Woven Sacks project?
- What is the Manufacturing Process and Formulations of a HDPE/PP Woven Sacks Business?
- What is the total size of land required for setting up a HDPE/PP Woven Sacks Manufacturing plant?
- What will be the income and expenditures for a HDPE/PP Woven Sacks Manufacturing plant?
- What are the Projected Balance Sheets of a HDPE/PP Woven Sacks Manufacturing plant?
- What are the requirement of utilities and overheads for setting up a HDPE/PP Woven Sacks project?
- What is the Built up Area Requirement and cost for setting up a HDPE/PP Woven Sacks Business?
- What are the Personnel (Manpower) Requirements for setting up a HDPE/PP Woven Sacks Business
- What are Statistics of Import & Export for HDPE/PP Woven Sacks?
- What is the time required to break-even?
- What is the Break-Even Analysis of a HDPE/PP Woven Sacks Manufacturing plant?
- What are the Project financials of a HDPE/PP Woven Sacks Manufacturing plant?
- What are the Profitability Ratios of a HDPE/PP Woven Sacks Manufacturing plant?
- What is the Sensitivity Analysis-Price/Volume of a HDPE/PP Woven Sacks Manufacturing plant?
- What are the Projected Pay-Back Period and IRR of a HDPE/PP Woven Sacks Manufacturing plant?
Market Outlook
The global demand for polypropylene woven bags and sacks is projected to develop at a CAGR of 4.2 percent over the next five years. Polypropylene woven bags and sacks are used in a variety of industries.
Polypropylene woven bags and sacks are widely used in agriculture, food processing, geotechnical packaging, tourism and transportation, everyday necessities, and flood control devices, to name a few.

Key Players
- Abdos Polymers Ltd.
- Berry Global, Inc.
- Emmbi Industries Limited
- Al-Tawfiq Company
- Muscat Polymers Pvt. Ltd.
- Mondi Group plc
- Palmetto Industries
- Printpak Inc.
- United Bags, Inc.
- Uflex Ltd.