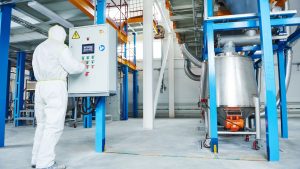
The chemical industry contracted slightly during the pandemic recession. Chemical companies have had to cut costs and streamline operations - nearly all have reduced staff, sold off non-essential assets, and are planning to reduce capacity if economic conditions persist. New opportunities are opening up driven by shifts in demand and new technologies. Chemicals are a diverse bunch of goods, including everything from cleaners and paints, to plastics and packaging.
And according to the US Commerce Department, during the pandemic recession the chemicals industry contracted slightly—at that time demand for some goods was down—but new opportunities are opening up in this field.
Visit this Page for More Information: Start a Business in Chemical Industry Projects
The chemicals industry is comprised of four major divisions: specialty chemicals (including agrochemicals) being the largest and second largest, with pharmaceuticals and cosmetics accounting for a relatively small market share. Over the last few years, in the face of falling prices and demand, the chemicals industry has been hit by an extraordinary contraction with revenues sinking to about $10 billion in 2010. The economy has begun to pick up again so that business prospects have brightened to some extent.
This article will discuss the opportunities and challenges of the chemical industry. It also emphasizes on how to tackle the challenges, as well as how to take advantage of the opportunities within the industry.
Read Similar Articles: Chemical Industry
Challenges
Price Hike- The biggest challenge that many countries face is the wide variance in energy prices across borders. Energy prices are different in various countries due to several reasons, including different labour wages, participation of local companies in import activities, and others. Would you believe that the energy rate paid by two neighbouring European nations could be as much as 30 percent higher than the other?
For chemical manufacturers, the last decade has been a difficult one. As the cost of energy escalated, it became harder and harder to pass these costs along to consumers. You see, in order for your company to succeed over the long term, it needs to ensure its prices are at or below the competitions. Now that energy prices have decreased, this is an opportune time to reassess how you structure your chemicals sales contracts.
Watch Video: India's Chemical Industry: Sector Overview
Managing Data
Chemical companies have to manage a large amount of operational, financial and production data. Otherwise, they won’t meet their customers’ requirement in innovative products and timely supply. But the current industry is facing increasing pressure on quality and cost-down, that makes it hard to manage these data manually.
Chemical companies are responsible for large amounts of data that are produced in the production and operational process. Data generated in these processes is protected by Intellectual Property (IP). This data is important to manufacturers and is valuable to their trading partners. Chemical companies need to view and use this data differently, such as viewing operating parameters and monitoring up-time of equipment.
Cost Cutting:
Cutting down formula costs is critical to a manufacturer's bottom line. However, providing this data manually to suppliers can be time-consuming and increases the risk of errors. Six Sigma Blackbelt ePCR provides instant access to purchase requirements, manufacturing quality standards, contracts and performance previously held only in hardcopy documents. It also manages inventory levels, cost of goods sold, compliance with supplier agreements and product specifications.
Related Feasibility Study Reports: Chemicals (Organic, Inorganic, Industrial) Projects
Optima Corporation excels in custom manufacturing solutions that meet the tightest of deadlines. Our chemists take advantage of volume and other discounts to optimize costs and invent new efficiencies. We also offer competitive tiered pricing to reduce costs based on agreed-upon volumes.
As an important part of the world manufacturing economy, chemical companies depend on a steady stream of raw materials, as well as the ability to make certain ingredients at scale. Keep this in mind when making material sourcing decisions related to formulas you develop for your company's products.
Decrease in Suppliers:
Salt of the Earth has trusted Synthos to supply the required raw materials for their main product line. Synthos is also an active partner with Salt of the Earth in formulating new and innovative solutions to further reduce costs as well as strengthen its presence in emerging markets. Nowadays there is a decrease in suppliers visible due to lockdown and other formalities imposed on the workflow.
Suppliers of raw and bulk chemicals often require a minimum business commitment, which limits manufacturers' ability to change vendors based on fluctuating demand patterns. The Spot Price Index (SPI) offers end-users real-time pricing intelligence, monitoring global market trends and helping to find new opportunities and optimize inventory levels.
Read our Books Here: Chemical Technology (Organic, Inorganic, and Industrial), Fine Chemicals
Opportunities:
Better Strategies and Planning- The global chemicals industry has been in a state of decline since 2009 -- the worst period for the industry since the late 1990s. However, a turnaround is underway driven by steady increases in oil prices, stemming from improved demand and investment in new production capacity in the Middle East Gulf areas. Most of this growth will come from its core business: petrochemicals and basic industries. Also, chemicals producers are beginning to shift their strategy to focus more on supplying high value-added semi-finished and finished products to niche markets. A strong push for continuous innovation is emerging in almost all segments as producers capitalize on new technologies to design low cost, high value products that respond better to customer needs."
Improvement- The chemicals industry helps to improve practically every aspect of our lives, from the clothes we wear, to the food we eat, to the drugs that make us better. With high margins and low capital investment requirements, it is one of the most attractive markets for new entrants into manufacturing. For the first time, CRX releases an in-depth report detailing the global chemicals performance by subsector, geography and chemicals type. The report identifies problems and opportunities in a highly fragmented industry to help you make better-informed decisions. It gives you detailed insight into:
Positive Response- The global outlook for chemicals production is positive. Growth predicted by most analysts, especially for China and emerging economies. The BASF chemical company expects to grow 4.4% in 2021 and this is above average for the years prior to the coronavirus pandemic and represents a strong rebound following the pandemic recession where overall global chemical production contracted by 0.4% in 2020, (compared to an increase of 1.9% in 2019).
Download PDF: India's Chemical Industry: Sector Overview
Increase in Production- Global chemical production is forecast to increase by over 4% in 2021, representing a post-pandemic rebound compared to pre-pandemic rates of 0.4% decline (in 2020). Chemicals are the basis of 'essentials' – our modern life and standard of living. BASF shared its global growth outlook for chemical production today in conjunction with the release of its annual corporate report, Annual Report 2014.
Faster Growth- Global chemical production is growing at a faster rate according to most analysts. The petrochemical industry boosted output 8.8% over the last year, and its demand far outstrips current supply. Chemicals derived from natural gas are the fastest growing segment in the industry, with initiatives in China and North America driving demand for ethylene and propylene. Rubber resins, which increased by 6.2% in recent months, continue to be a large growth market due to rising demand for automobile tires in China and India. BASF predicts that refrigeration chemicals will lead the world chemical industry out of recession as demand for cold storage continues to increase across emerging markets such as India, Indonesia and Malaysia.
The company also forecasts steady growth for all sectors apart from pharmaceuticals, which is expected to decline due to stricter laws on price controls that have been implemented by governments in Europe. Chemical companies are financing research into new processes and technologies necessary for efficient production of environmentally-friendly products that meet consumer demands for organic food.
New Projects- It is projected these emerging economies will become major originators of chemicals, plastics and rubber chemicals. By 2021 a major portion of these products will still be exported, but some of this capacity will expand to meet domestic and regional demand as well. This overall increase in global chemical production combined with the need for chemicals that have higher value will have multiple implications for producers, including: pricing power for select products, increasing potential for synergy and strategic opportunities with other BASF business units.
Watch other Informative Videos: Chemicals (Organic, Inorganic, and Industrial)
Conclusion:
Chemical production is a vital component of the global economy. Synthetic materials and products derived from them have been used for centuries, since the early days of farming. Industrial chemicals are essential for a variety of manufacturing processes and can be derived naturally (e.g., vegetable oils) or manufactured in a lab (inorganic chemicals). These chemicals can be found in all products: food, water, clothes, toys, and cosmetics.
BASF is a German chemical company, with production sites in over 90 countries. Their products are sold to more than one hundred thousand customers. In 2014, BASF posted sales of about $67 billion and income of approximately $11 billion. BASF Chemical Co. is a chemical company headquartered in Munich, Germany. It was founded on December 6, 1865.
It is the world's largest chemical producer based on revenue (42.4 billion euros in 2011), and has operations on five continents. BASF has about 112,000 employees and had sales of $60.4 billion in 2008. Things have been going so well for decades. Everything was in place, and respected its place. Even the environment was looking great, and new green technologies were keeping it that way. Then everything changed. All at once.
See More Links:
· Start a Business in Asia
· Start a Business in Potential Countries for Doing Business
· Best Industry for Doing Business
· Business Ideas with Low, Medium & High Investment
· Looking for Most Demandable Business Ideas for Startups
· Startup Consulting Services
· Start a Business in Africa
· Start a Business in India
· Start a Business in Middle East
· Related Videos
· Related Books
· Related Projects
· Related Market Research Reports
𝐂𝐨𝐧𝐭𝐚𝐜𝐭 𝐮𝐬
NIIR PROJECT CONSULTANCY SERVICES, DELHI
An ISO 9001:2015 Company
ENTREPRENEUR INDIA
106-E, Kamla Nagar, Opp. Mall ST,
New Delhi-110007, India.
Email: npcs.ei@gmail.com
info@entrepreneurindia.co
Tel: +91-11-23843955, 23845654, 23845886
Mobile: +91-9097075054, 8800733955
Website: https://www.entrepreneurindia.co
https://www.niir.org